Az SMT tapasz és a THT részletes elemzése a lyukba dugható PCBA három anti-festő bevonat folyamat és kulcsfontosságú technológiák segítségével!
Ahogy a PCBA komponensek mérete egyre kisebb lesz, a sűrűség egyre nagyobb lesz; Egyre kisebb az eszközök és eszközök közötti támasztómagasság (a NYÁK és a hasmagasság közötti távolság), valamint a környezeti tényezők PCBA-ra gyakorolt hatása is növekszik. Ezért magasabb követelményeket támasztunk az elektronikai termékek PCBA-jának megbízhatóságára vonatkozóan.
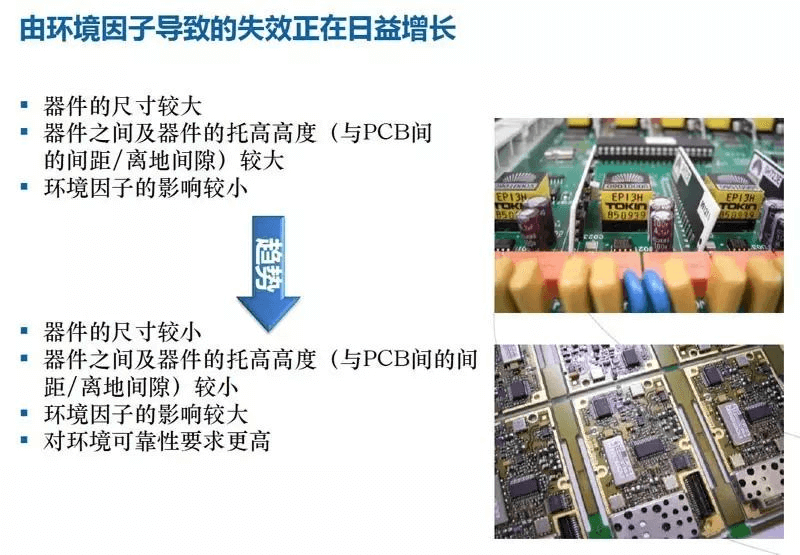
1.Környezeti tényezők és hatásuk
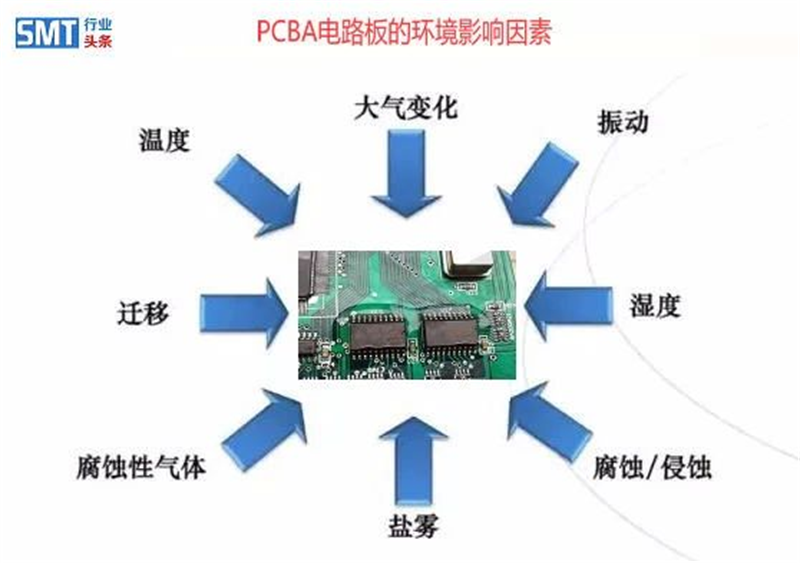
Az olyan általános környezeti tényezők, mint a páratartalom, por, sópermet, penész stb., a PCBA különböző meghibásodási problémáit okozhatják
Nedvesség
A külső környezetben található elektronikus PCB-elemek szinte mindegyike ki van téve a korrózió veszélyének, amelyek közül a víz a legfontosabb korróziós közeg. A vízmolekulák elég kicsik ahhoz, hogy behatoljanak egyes polimer anyagok hálós molekuláris résébe, és bejussanak a belsejébe, vagy a bevonat tűlyukon keresztül elérjék az alatta lévő fémet, hogy korróziót okozzanak. Amikor a légkör elér egy bizonyos páratartalmat, ez PCB elektrokémiai migrációt, szivárgási áramot és jeltorzulást okozhat a nagyfrekvenciás áramkörben.
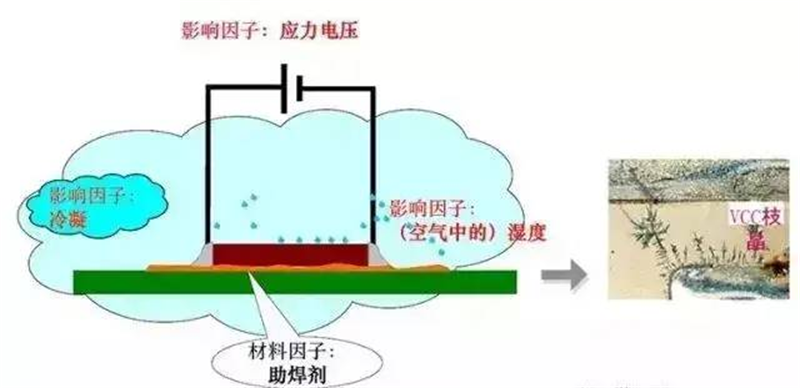
Gőz/nedvesség + ionos szennyeződések (sók, fluxus aktív szerek) = vezető elektrolitok + feszültség feszültség = elektrokémiai migráció
Amikor a relatív páratartalom a légkörben eléri a 80%-ot, 5-20 molekula vastagságú vízréteg alakul ki, és mindenféle molekula szabadon mozoghat. Ha szén van jelen, elektrokémiai reakciók léphetnek fel.
Amikor a relatív páratartalom eléri a 60%-ot, a berendezés felületi rétege 2-4 vízmolekula vastagságú vízréteget képez, ha szennyező anyagok feloldódnak benne, kémiai reakciók lépnek fel;
Ha a relatív páratartalom < 20% a légkörben, szinte minden korróziós jelenség megszűnik.
Ezért a nedvességállóság a termékvédelem fontos része.
Az elektronikus eszközök esetében a nedvesség három formában jelentkezik: eső, páralecsapódás és vízgőz. A víz egy elektrolit, amely nagy mennyiségű korrozív iont old fel, amelyek korrodálják a fémeket. Ha a berendezés egy bizonyos részének hőmérséklete a "harmatpont" (hőmérséklet) alatt van, akkor a felületen páralecsapódás keletkezik: szerkezeti részek vagy PCBA.
Por
A légkörben por van, a por által adszorbeált ionszennyező anyagok megtelepednek az elektronikus berendezések belsejében, és meghibásodást okoznak. Ez gyakori probléma a terepen előforduló elektronikai hibáknál.
A por két típusra oszlik: a durva por 2,5-15 mikron szabálytalan részecskék átmérője, általában nem okoz hibát, ívet és egyéb problémákat, de hatással van a csatlakozó érintkezésére; A finom por szabálytalan, 2,5 mikronnál kisebb átmérőjű részecskék. A finom por bizonyos tapadást mutat a PCBA-n (furnér), amelyet csak antisztatikus kefével lehet eltávolítani.
A por veszélyei: a. A PCBA felületén leülepedő por miatt elektrokémiai korrózió keletkezik, és a meghibásodási arány nő; b. A por + párás hő + só köd okozta a legnagyobb károkat a PCBA-ban, az elektronikai berendezések meghibásodása pedig a vegyiparban és a part közelében, a sivatagban (szikes-lúgos föld), valamint a Huaihe folyó déli részén volt a legnagyobb a penész-, ill. esős évszak.
Ezért a porvédelem fontos része a terméknek.
Só spray
A sópermet kialakulása:A sópermetet olyan természetes tényezők okozzák, mint az óceán hullámai, árapály, légköri keringési (monszun) nyomás, napsütés és így tovább. A széllel befelé sodródik, koncentrációja a parttól való távolság előrehaladtával csökken. Általában a sópermet koncentrációja a part 1%-a, ha az 1 km-re van a parttól (de a tájfun időszakban messzebbre is fúj).
A sópermet káros hatásai:a. károsítsa a fém szerkezeti részek bevonatát; b. Az elektrokémiai korróziós sebesség felgyorsulása a fémhuzalok töréséhez és az alkatrészek meghibásodásához vezet.
Hasonló korróziós források:a. A kézi izzadság sót, karbamidot, tejsavat és egyéb vegyi anyagokat tartalmaz, amelyek ugyanolyan maró hatást fejtenek ki az elektronikus berendezésekre, mint a sóspray. Ezért az összeszerelés vagy használat során kesztyűt kell viselni, és a bevonatot nem szabad puszta kézzel megérinteni; b. Halogének és savak vannak a fluxusban, amelyeket meg kell tisztítani és ellenőrizni kell a maradék koncentrációjukat.
Ezért a sópermet megelőzése fontos része a termékek védelmének.
Forma
A penész, a fonalas gombák általános neve, jelentése "penészes gombák", amelyek hajlamosak buja micéliumot képezni, de nem hoznak létre olyan nagy termőtesteket, mint a gombák. Nedves és meleg helyeken szabad szemmel sok tárgy megnő a homályos, pelyhes vagy pókháló alakú telepek közül, azaz a penész.
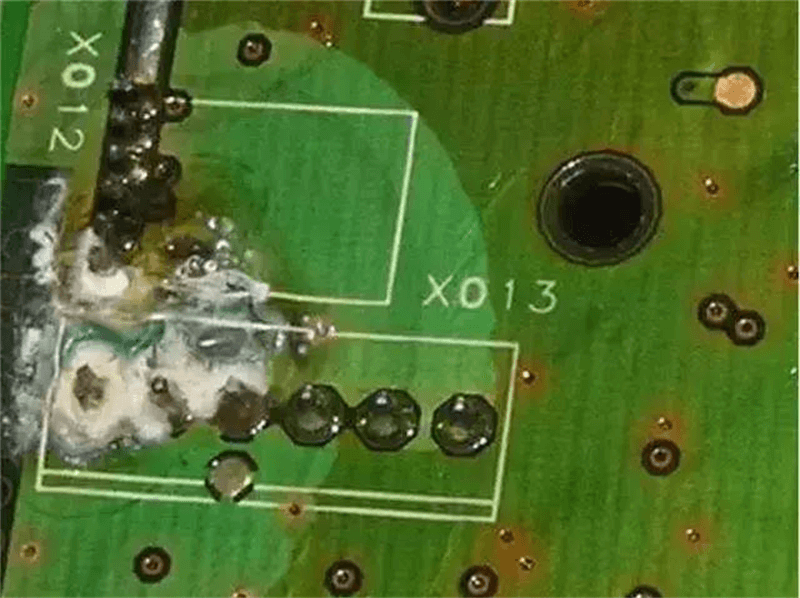
FÜGE. 5: PCB penészgomba jelenség
A penész károsodása: a. a penészfagocitózis és a szaporodás a szerves anyagok szigetelését csökkenti, károsítja és tönkreteszi; b. A penész anyagcseretermékei szerves savak, amelyek befolyásolják a szigetelést és az elektromos szilárdságot, és elektromos ívet hoznak létre.
Ezért a penész elleni védelem fontos része a védőszereknek.
A fenti szempontokat figyelembe véve a termék megbízhatóságát jobban kell garantálni, a lehető legalacsonyabbra kell szigetelni a külső környezettől, így kerül bevezetésre a formabevonat eljárás.
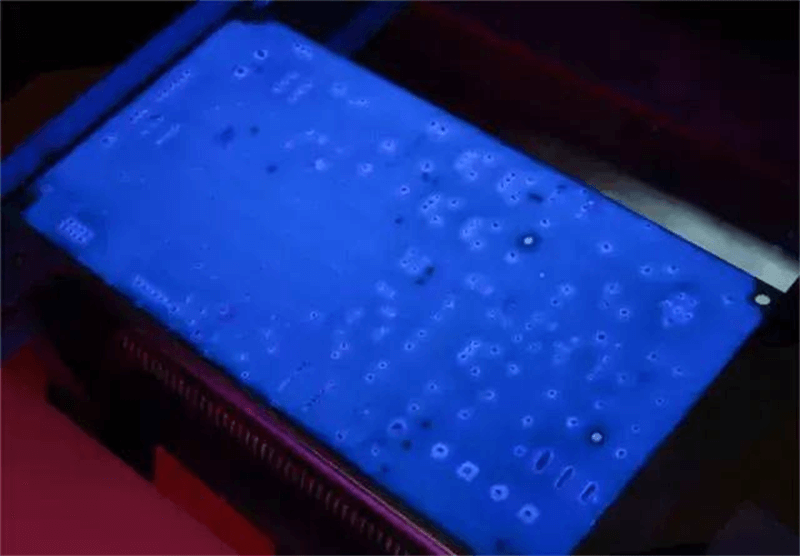
A PCB bevonása a bevonási folyamat után, a lila lámpa lövési hatása alatt az eredeti bevonat olyan szép lehet!
Három festésgátló bevonatA NYÁK felületén vékony védőszigetelő réteg bevonására utal. Jelenleg ez a leggyakrabban használt hegesztés utáni bevonási módszer, amelyet néha felületi bevonatnak és konform bevonatnak is neveznek (angol nevén: coating, conformal coating). Elszigeteli az érzékeny elektronikus alkatrészeket a zord környezettől, nagymértékben javíthatja az elektronikai termékek biztonságát és megbízhatóságát, és meghosszabbíthatja a termékek élettartamát. Három festésgátló bevonat megvédheti az áramkört/alkatrészeket a környezeti tényezőktől, például nedvességtől, szennyeződésektől, korróziótól, stressztől, ütéstől, mechanikai vibrációtól és hőciklustól, miközben javítja a termék mechanikai szilárdságát és szigetelési jellemzőit.
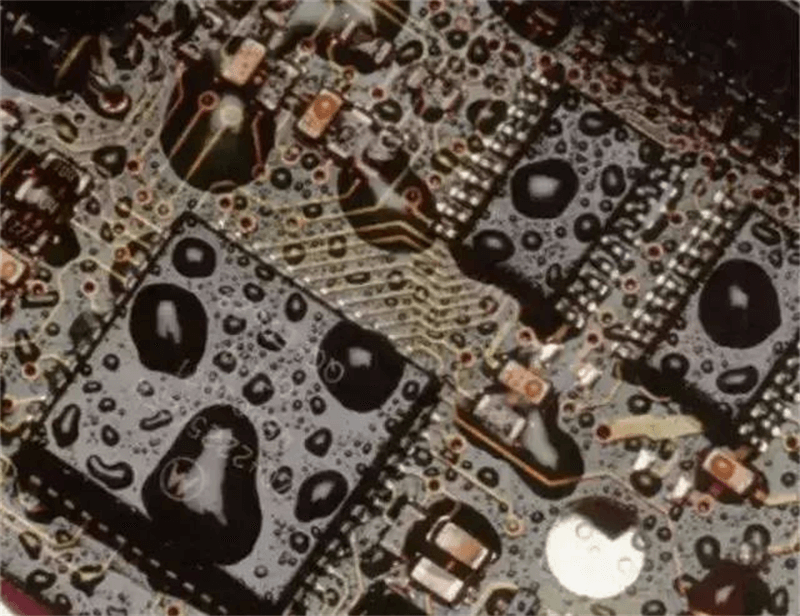
A PCB bevonási folyamata után átlátszó védőfóliát hozzon létre a felületen, hatékonyan megakadályozza a víz és a nedvesség behatolását, elkerülje a szivárgást és a rövidzárlatot.
2. A bevonási folyamat főbb pontjai
Az IPC-A-610E (Electronic Assembly Testing Standard) követelményei szerint ez elsősorban a következő szempontokban tükröződik:
Régió
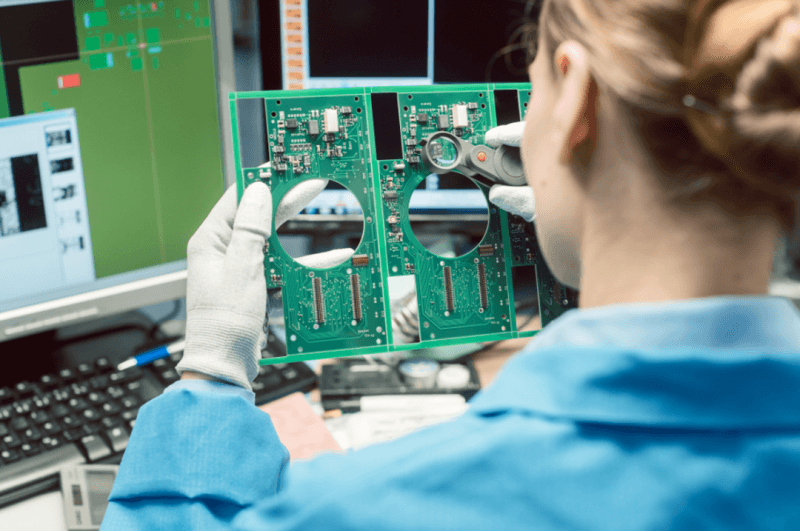
1. Nem bevonható területek:
Elektromos csatlakozást igénylő területek, például aranypárnák, arany ujjak, fém átmenő lyukak, tesztfuratok;
Elemek és akkumulátorrögzítők;
Csatlakozó;
Biztosíték és ház;
Hőelvezető készülék;
áthidaló vezeték;
Optikai eszköz lencséje;
Potenciométer;
Érzékelő;
Nincs lezárt kapcsoló;
Egyéb területek, ahol a bevonat befolyásolhatja a teljesítményt vagy a működést.
2. Bevonandó területek: minden forrasztási csatlakozás, csap, alkatrész és vezeték.
3. Választható területek
Vastagság
A vastagságot a nyomtatott áramköri alkatrész sík, akadálytalan, kikeményedett felületén vagy egy csatolt lemezen mérik, amelyen az alkatrészrel együtt dolgoznak. A rögzített táblák ugyanabból az anyagból készülhetnek, mint a nyomtatott táblák vagy más nem porózus anyagok, például fém vagy üveg. A nedves rétegvastagság mérése a bevonatvastagság mérésének opcionális módszereként is használható, amennyiben dokumentált konverziós összefüggés van a nedves és száraz rétegvastagság között.

1. táblázat: A vastagsági tartomány szabványa minden bevonóanyag-típushoz
A vastagság vizsgálati módszere:
1. Száraz rétegvastagság mérő eszköz: mikrométer (IPC-CC-830B); b Száraz filmvastagság-mérő (vas alap)
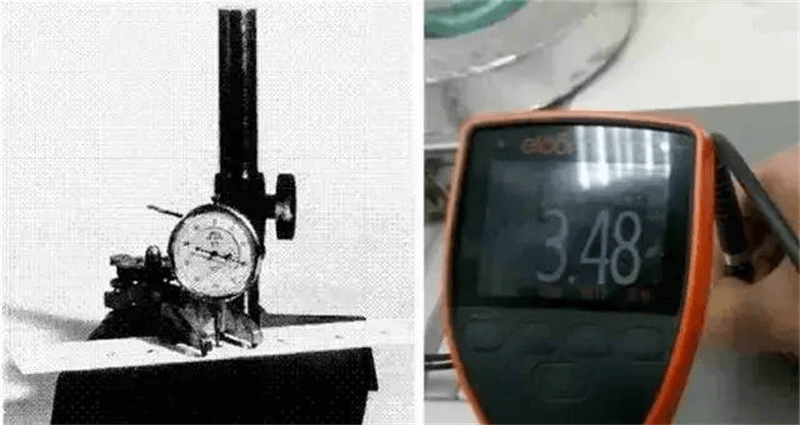
9. ábra Mikrométeres szárazfilm-készülék
2. Nedves rétegvastagság mérés: a nedves film vastagsága nedves rétegvastagság-mérő műszerrel meghatározható, majd a ragasztó szilárdanyag-tartalmának arányával számítható ki.
A száraz film vastagsága
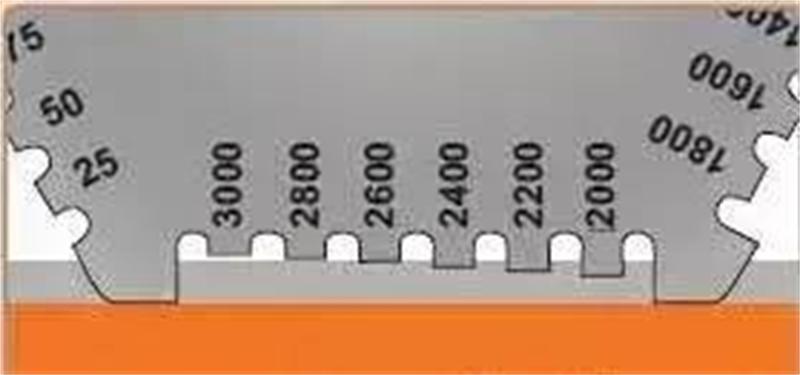
ábrán látható. 10, a nedves rétegvastagságot a nedves rétegvastagság-mérővel határoztuk meg, majd kiszámítottuk a száraz rétegvastagságot
Élfelbontás
Meghatározás: Normál körülmények között a permetezőszelep permetezése a vonal szélén nem lesz túl egyenes, mindig lesz egy bizonyos sorja. A sorja szélességét élfelbontásként definiáljuk. Az alábbiak szerint a d mérete az élfelbontás értéke.
Megjegyzés: Az élfelbontás minden bizonnyal minél kisebb, annál jobb, de a különböző vásárlói igények nem azonosak, így az adott bevont élfelbontás mindaddig, amíg megfelel az ügyfelek igényeinek.

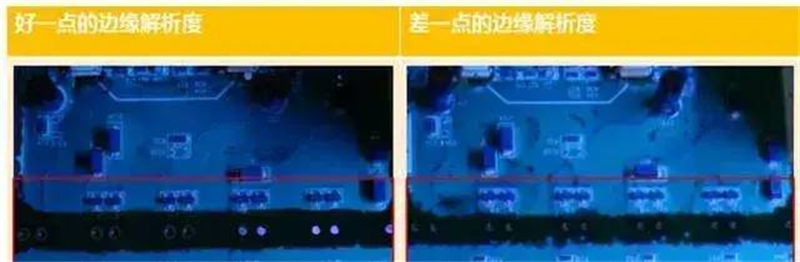
11. ábra: Élfelbontás összehasonlítása
Egyöntetűség
A ragasztónak egyenletes vastagságúnak és sima és átlátszó fóliának kell lennie a termékben, a hangsúly a termékben lévő ragasztó egyenletességén van a terület felett, akkor azonos vastagságúnak kell lennie, nincs folyamatprobléma: repedések, rétegződés, narancssárga vonalak, szennyezés, kapilláris jelenség, buborékok.
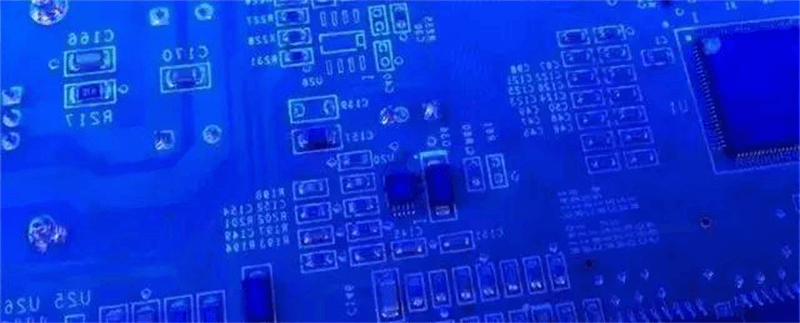
12. ábra: Axiális automatikus AC sorozatú automatikus bevonógép bevonat hatása, az egyenletesség nagyon következetes
3. Bevonási folyamat megvalósítása
Bevonási folyamat
1 Készítse elő
Készítsen termékeket, ragasztót és egyéb szükséges tárgyakat;
Határozza meg a helyi védelem helyét;
Határozza meg a legfontosabb folyamat részleteit
2: Mosás
A hegesztés után a legrövidebb időn belül meg kell tisztítani, a hegesztési szennyeződések elkerülése érdekében nehéz tisztítani;
A megfelelő tisztítószer kiválasztásához határozza meg, hogy a fő szennyezőanyag poláris vagy nem poláris;
Alkoholos tisztítószer használata esetén ügyelni kell a biztonsági szempontokra: a mosás után megfelelő szellőzésre, hűtési és szárítási szabályokra van szükség, hogy elkerüljük a sütőben történő robbanás okozta maradék oldószer elpárolgást;
Vizes tisztítás, lúgos tisztítófolyadékkal (emulzió) a folyasztószer mosásához, majd tiszta vízzel öblítse le a tisztítófolyadék tisztításához, hogy megfeleljen a tisztítási szabványoknak;
3. Maszkolás elleni védelem (ha nem használunk szelektív bevonó berendezést), azaz maszk;
Meg kell választani a nem tapadó fólia nem fogja át a papírszalagot;
Az IC védelemhez antisztatikus papírszalagot kell használni;
A rajzok követelményei szerint egyes eszközök árnyékolására;
4. Párátlanítás
Tisztítás után az árnyékolt PCBA-t (alkatrészt) elő kell szárítani és párátlanítani a bevonat előtt;
Határozza meg az előszárítás hőmérsékletét/idejét a PCBA (komponens) által megengedett hőmérséklet szerint;
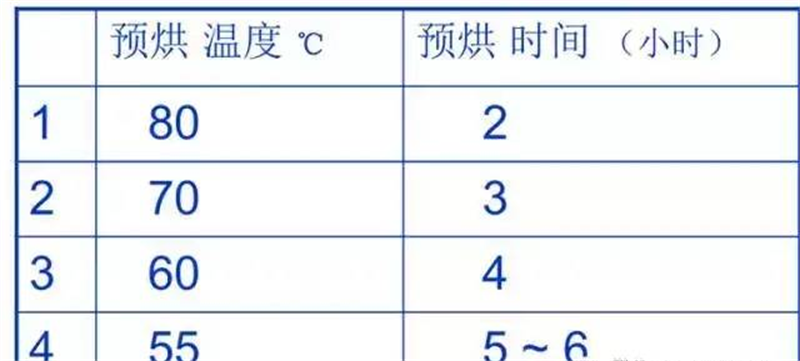
A PCBA (komponens) meghatározhatja az előszárítási táblázat hőmérsékletét/idejét
5 Kabát
Az alakbevonás folyamata a PCBA védelmi követelményektől, a meglévő technológiai berendezésektől és a meglévő műszaki tartaléktól függ, amit általában a következő módokon érnek el:
a. Ecset kézzel
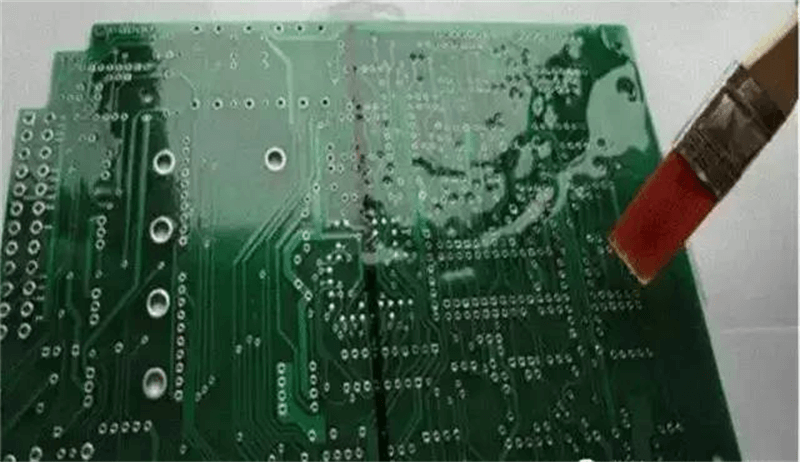
13. ábra: Kézi fogmosási módszer
Az ecsetbevonat a legszélesebb körben alkalmazható eljárás, alkalmas kis tételes gyártásra, PCBA szerkezetű összetett és sűrű, meg kell védeni a kemény termékek védelmi követelményeit. Mert az ecsetbevonat szabadon szabályozható, így a nem festhető részek nem szennyeződnek;
Az ecsetbevonat a legkevesebb anyagot fogyasztja, megfelel a kétkomponensű festék magasabb árának;
A festési folyamat magas követelményeket támaszt a kezelővel szemben. Az építés előtt gondosan meg kell emészteni a rajzokat és a bevonattal kapcsolatos követelményeket, fel kell ismerni a PCBA-komponensek nevét, és fel kell tüntetni a nem bevonható részeket figyelemfelkeltő jelzésekkel;
Az üzemeltetők a szennyeződés elkerülése érdekében soha nem érinthetik meg a kezükkel a nyomtatott beépülő modult;
b. Merítsen kézzel
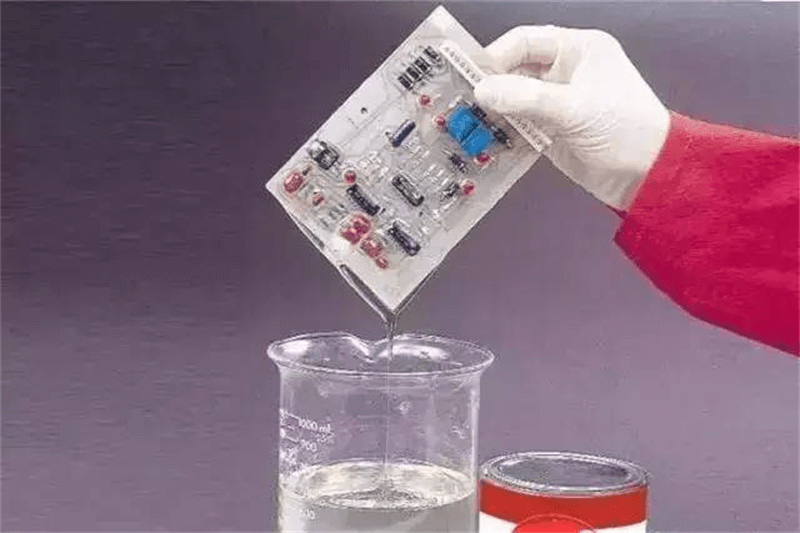
14. ábra: Kézi mártással történő bevonási módszer
A bemerítési eljárás biztosítja a legjobb bevonási eredményt. Egységes, folyamatos bevonat alkalmazható a PCBA bármely részére. A bemerítési eljárás nem alkalmas állítható kondenzátorokkal, finomhangoló mágneses magokkal, potenciométerekkel, csésze alakú mágneses magokkal és egyes rossz tömítésű alkatrészekkel rendelkező PC-k esetén.
A bemerítési folyamat fő paraméterei:
Állítsa be a megfelelő viszkozitást;
Szabályozza a PCBA emelési sebességét, hogy megakadályozza a buborékok képződését. Általában nem több, mint 1 méter másodpercenként;
c. Permetezés
A permetezés a legszélesebb körben alkalmazott, könnyen elfogadott eljárási módszer, amely a következő két kategóriába sorolható:
① Kézi permetezés
15. ábra: Kézi permetezési módszer
Alkalmas a munkadarab bonyolultabb, nehéz támaszkodni az automatizálási berendezések tömeggyártási helyzetére, a termékcsaládra is alkalmas, de kevésbé helyzet, speciálisabb helyzetbe permetezhető.
Megjegyzés a kézi szóráshoz: a festékköd szennyezi egyes eszközöket, mint például a PCB-csatlakozó, az IC-aljzat, néhány érzékeny érintkező és néhány földelő rész, ezeknél az alkatrészeknél figyelni kell a menedékvédelem megbízhatóságára. Egy másik szempont, hogy a kezelő soha ne érintse meg a kezével a nyomtatott dugót, hogy elkerülje a dugó érintkezési felületének szennyeződését.
② Automatikus permetezés
Általában a szelektív bevonóberendezéssel végzett automatikus permetezésre utal. Tömeggyártásra alkalmas, jó konzisztencia, nagy pontosság, kevés környezetszennyezés. Az ipar korszerűsítésével, a munkaerőköltség növekedésével és a szigorú környezetvédelmi követelményekkel az automatikus permetezőberendezések fokozatosan felváltják a többi bevonási módszert.
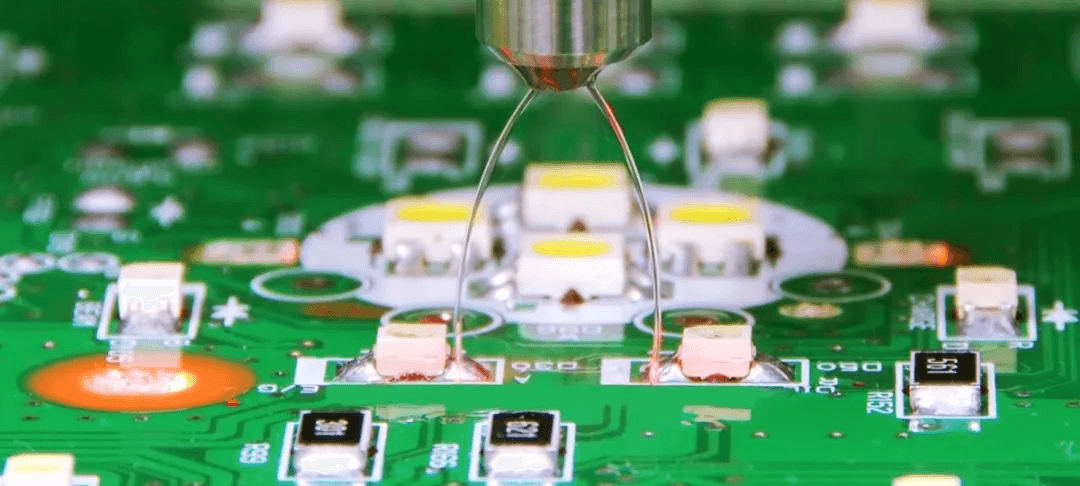
Az ipar 4.0 növekvő automatizálási követelményeivel az ipar fókusza a megfelelő bevonóberendezések biztosításáról a teljes bevonási folyamat problémájának megoldására helyeződött át. Automatikus szelektív bevonógép - a bevonat pontos és anyagpazarlás nélkül, alkalmas nagy mennyiségű bevonathoz, leginkább három festék elleni bevonat nagy mennyiségéhez.
Összehasonlításaautomatikus bevonógépéshagyományos bevonási eljárás
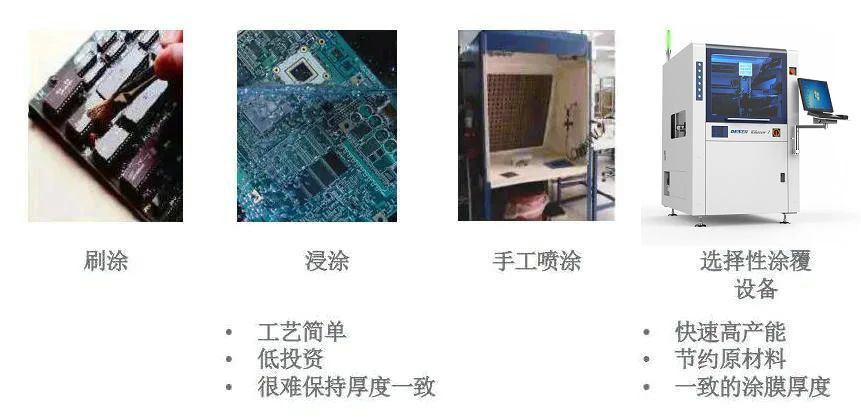
Hagyományos PCBA háromálló festékbevonat:
1) Ecset bevonat: vannak buborékok, hullámok, kefe szőrtelenítés;
2) Írás: túl lassú, a pontosság nem szabályozható;
3) Az egész darab beáztatása: túl pazarló festék, lassú sebesség;
4) Szórópisztoly permetezés: a rögzítés védelmére, túlságosan sodródik
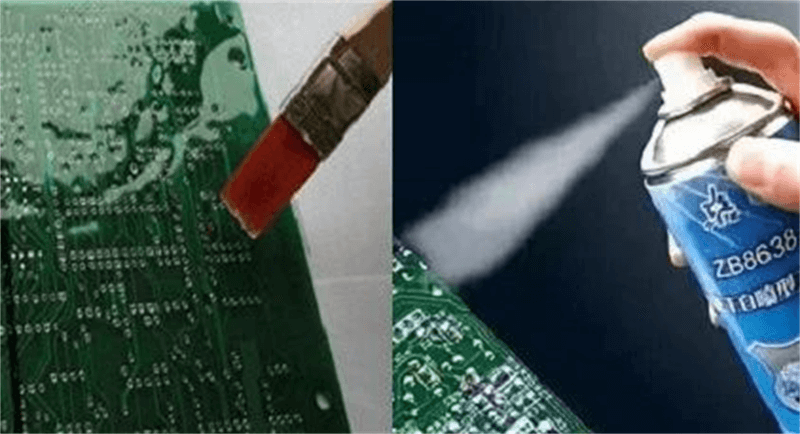
Bevonógép bevonat:
1) A szórófestés mennyisége, a szórófestés helyzete és területe pontosan be van állítva, és nincs szükség emberek hozzáadására a tábla törléséhez a szórófestés után.
2) Néhány, a lemez szélétől nagy távolságra lévő dugaszolható alkatrész közvetlenül festhető a szerelvény felszerelése nélkül, megkímélve a lemezbeállító személyzetet.
3) Nincs gáz elpárologtatás, a tiszta működési környezet biztosítása érdekében.
4) Az összes hordozófelületen nem kell rögzítőelemeket használni a szénfilm lefedéséhez, így elkerülhető az ütközés.
5) Három egyenletes festékrétegvastagság, nagymértékben javítja a termelés hatékonyságát és a termékminőséget, de elkerüli a festékpazarlást is.
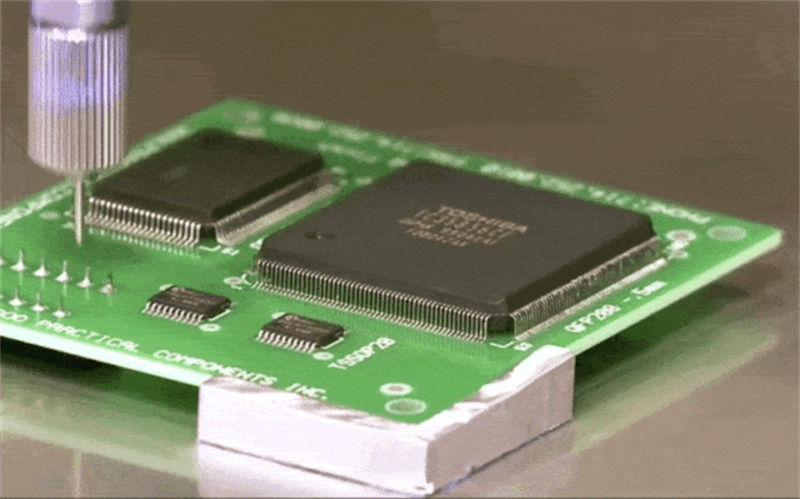
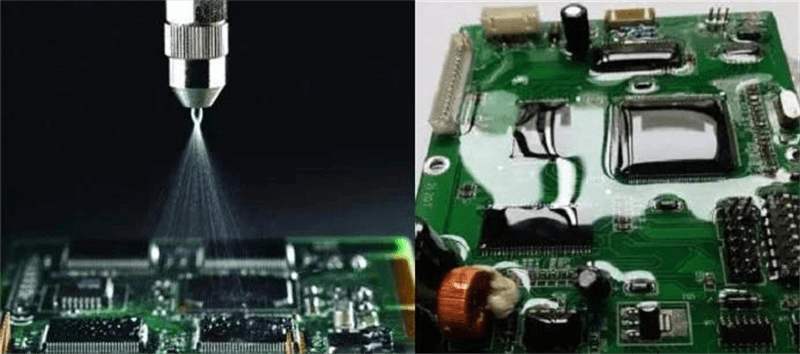
PCBA automatikus három festék elleni bevonógép, kifejezetten három festék elleni intelligens szóróberendezés permetezésére tervezték. Mivel a permetezendő anyag és az alkalmazott permetezőfolyadék eltérő, a berendezés alkatrészeinek kiválasztásában használt bevonógép is eltérő, három festékgátló bevonógép a legújabb számítógépes vezérlőprogramot alkalmazza, és megvalósíthatja a háromtengelyes kapcsolatot, egyidejűleg kamera pozicionáló és nyomkövető rendszerrel felszerelt, pontosan tudja szabályozni a permetezési területet.
Három festékgátló bevonógép, más néven három festékgátló ragasztógép, három festékszóró ragasztógép, három festék elleni olajszóró gép, három festék elleni festékszóró gép, kifejezetten folyadékvezérlésre szolgál, a PCB felületén borított egy réteg három anti-festék, mint például impregnálás, szórással vagy centrifugálás módszerrel a PCB felületén borított egy réteg fotoreziszt.
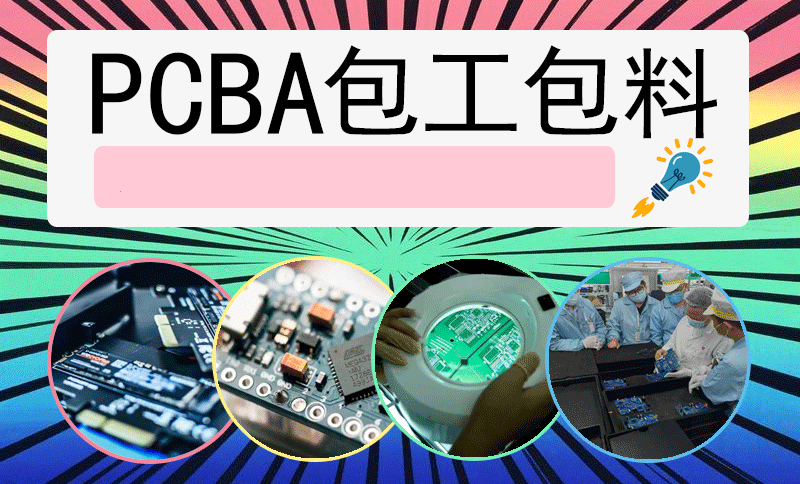
Hogyan lehet megoldani az új korszak három anti festék bevonat kereslet, vált sürgős probléma megoldani az iparban. A precíziós szelektív bevonógép által képviselt automatikus bevonóberendezés új működési módot hoz,bevonat pontos és nem pazarló anyag, a legalkalmasabb a nagyszámú három anti-festés bevonat.