【 Száraz áruk 】 Az SMT mélyreható elemzése, miért érdemes vörös ragasztót használni? (2023 Essence Edition), megérdemled!
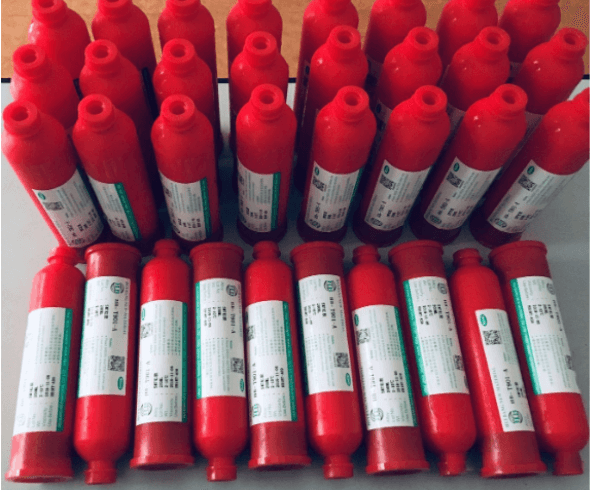
Az SMT ragasztó, más néven SMT ragasztó, SMT vörös ragasztó, általában egy piros (sárga vagy fehér) paszta, egyenletesen eloszlatva keményítővel, pigmenttel, oldószerrel és egyéb ragasztókkal, főként alkatrészek nyomdalapon történő rögzítésére szolgál, általában adagolással elosztva. vagy acélszitanyomási módszerek. Az alkatrészek rögzítése után helyezze őket a kemencébe vagy a visszafolyó kemencébe melegítés és keményedés céljából. A különbség a forrasztópasztától az, hogy hő hatására kikeményedik, fagyáspontja 150°C, és újramelegítés után sem oldódik fel, vagyis a tapasz hőkeményedési folyamata visszafordíthatatlan. Az SMT ragasztó használati hatása a hőkezelési feltételektől, a csatlakoztatott tárgytól, a használt berendezéstől és a működési környezettől függően változik. A ragasztót a nyomtatott áramköri kártya összeszerelési eljárásának (PCBA, PCA) megfelelően kell kiválasztani.
Az SMT tapasz ragasztó jellemzői, alkalmazása és kilátásai
Az SMT vörös ragasztó egyfajta polimer vegyület, a fő összetevők az alapanyag (azaz a fő nagy molekulatömegű anyag), a töltőanyag, a térhálósító szer, egyéb adalékok és így tovább. Az SMT vörös ragasztó viszkozitási folyékonysággal, hőmérsékleti jellemzőkkel, nedvesítési jellemzőkkel és így tovább. A vörös ragasztó ezen jellemzője szerint a gyártás során a vörös ragasztó használatának az a célja, hogy az alkatrészek szilárdan tapadjanak a NYÁK felületére, nehogy leessen. Ezért a tapasz ragasztó a nem alapvető technológiai termékek tiszta fogyasztása, és most a PCA tervezés és folyamat folyamatos fejlesztésével a lyukvisszafolyáson és a kétoldalas visszafolyó hegesztésen keresztül valósult meg, valamint a PCA rögzítési folyamata a tapasz ragasztó segítségével. egyre kevésbé tendenciát mutat.
Az SMT ragasztó használatának célja
① Akadályozza meg az alkatrészek leesését hullámforrasztáskor (hullámforrasztási eljárás). Hullámforrasztás alkalmazásakor az alkatrészeket a nyomtatott lapra rögzítik, hogy megakadályozzák az alkatrészek leesését, amikor a nyomtatott tábla áthalad a forrasztóhornyon.
② Akadályozza meg, hogy az alkatrészek másik oldala leessen az újrafolyós hegesztésnél (kétoldali visszafolyó hegesztési eljárás). A kétoldali visszafolyós hegesztésnél, hogy a forrasztott oldalon lévő nagyméretű eszközök ne essenek le a forraszanyag hőolvadása miatt, az SMT tapaszragasztót kell készíteni.
③ Akadályozza meg az alkatrészek elmozdulását és felállását (visszafolyó hegesztési eljárás, előbevonási eljárás). Visszafolyó hegesztési eljárásokban és előbevonatolási eljárásokban használják, hogy megakadályozzák az elmozdulást és az emelkedőt a szerelés során.
④ Jelölés (hullámforrasztás, visszafolyó hegesztés, előbevonás). Ezen túlmenően, amikor a nyomtatott táblákat és az alkatrészeket tételesen cserélik, tapasz ragasztót használnak a jelöléshez.
Az SMT ragasztót a felhasználási mód szerint osztályozzák
a) Kaparás típusa: a méretezés az acélháló nyomtatási és kaparási módjával történik. Ez a módszer a legszélesebb körben alkalmazott, és közvetlenül a forrasztópaszta-présen is használható. Az acélhálós lyukakat az alkatrészek típusa, az aljzat teljesítménye, vastagsága, valamint a lyukak mérete és alakja alapján kell meghatározni. Előnye a nagy sebesség, a nagy hatékonyság és az alacsony költség.
b) Adagolás típusa: A ragasztót adagoló berendezéssel hordják fel a nyomtatott áramköri lapra. Speciális adagolóberendezésre van szükség, és a költségek magasak. Az adagolóberendezés sűrített levegő használata, a vörös ragasztó a speciális adagolófejen keresztül a hordozóhoz, a ragasztási pont mérete, mennyi időre, a nyomócső átmérője és egyéb paraméterek ellenőrzése, az adagológép rugalmas funkcióval rendelkezik . A különböző alkatrészekhez különböző adagolófejeket használhatunk, beállíthatjuk a paramétereket a változtatáshoz, megváltoztathatjuk a ragasztópont alakját és mennyiségét is, a hatás elérése érdekében az előnyök kényelmesek, rugalmasak és stabilak. Hátránya, hogy könnyű a huzalhúzás és a buborékok. Beállíthatjuk a működési paramétereket, a sebességet, az időt, a légnyomást és a hőmérsékletet, hogy ezeket a hiányosságokat minimalizáljuk.
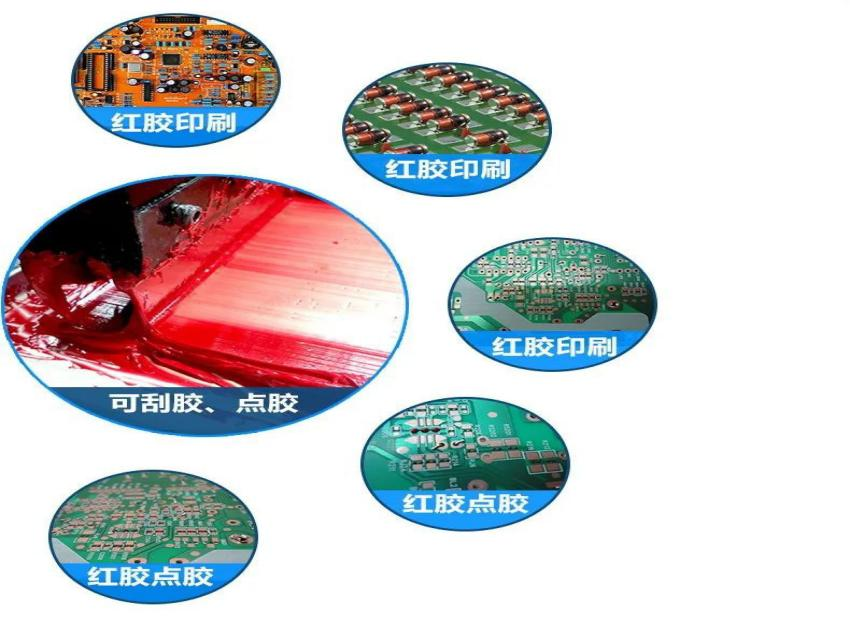
SMT tapasz ragasztó tipikus kötési feltételek
Kikeményedési hőmérséklet | Kötési idő |
100 ℃ | 5 perc |
120℃ | 150 másodperc |
150 ℃ | 60 másodperc |
Jegyzet:
1, minél magasabb a kikeményedési hőmérséklet és minél hosszabb a kikeményedési idő, annál erősebb a kötési szilárdság.
2, mivel a tapasz ragasztó hőmérséklete az aljzatrészek méretével és a szerelési helyzettel együtt változik, javasoljuk, hogy keresse meg a legmegfelelőbb keményedési feltételeket.
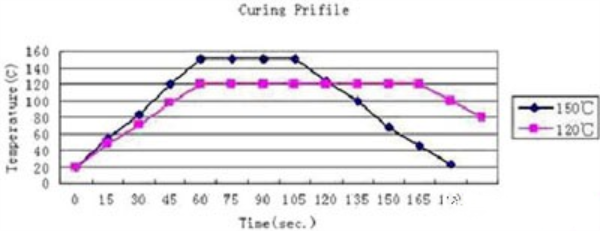
SMT javítások tárolása
Szobahőmérsékleten 7 napig, 5 °C alatti hőmérsékleten több mint 6 hónapig, 5 ~ 25 °C-on több mint 30 napig tárolható.
SMT ragasztókezelés
Mivel az SMT patch red ragasztót a hőmérséklet befolyásolja saját viszkozitásával, folyékonyságával, nedvesítésével és egyéb jellemzőivel, ezért az SMT patch red ragasztónak bizonyos használati feltételekkel és szabványos kezeléssel kell rendelkeznie.
1) A piros ragasztónak meghatározott áramlási számmal kell rendelkeznie, az adagolás számának, dátumának, típusának megfelelően.
2) A vörös ragasztót hűtőszekrényben 2 ~ 8 °C-on kell tárolni, hogy a hőmérsékletváltozás ne befolyásolja a jellemzőket.
3) A piros ragasztót 4 órán keresztül szobahőmérsékleten kell melegíteni, az első az elsőben felhasználás sorrendjében.
4) Az adagolási művelethez a tömlő piros ragasztóját le kell olvasztani, és a fel nem használt piros ragasztót vissza kell tenni a hűtőszekrénybe tárolásra, és a régi ragasztót és az új ragasztót nem lehet összekeverni.
5) A visszatérő hőmérséklet rögzítési űrlapjának, a visszatérő hőmérséklet személyének és a visszatérő hőmérsékleti időnek a pontos kitöltéséhez a felhasználónak használat előtt meg kell erősítenie a visszatérő hőmérséklet kitöltését. Általában a vörös ragasztó nem használható elavult.
Az SMT tapasz ragasztó folyamatjellemzői
Csatlakozási szilárdság: Az SMT ragasztónak erős csatlakozási szilárdságúnak kell lennie, megszilárdulás után még az olvadásponton sem válik le a forrasztóanyag.
Pöttyös bevonat: Jelenleg a nyomtatott táblák forgalmazási módja többnyire pontbevonat, így a ragasztónak a következő tulajdonságokkal kell rendelkeznie:
① Alkalmazkodni a különféle szerelési folyamatokhoz
Könnyen beállítható az egyes alkatrészek ellátása
③ Egyszerűen adaptálható az alkatrészfajták cseréjéhez
④ Stabil pontbevonat mennyisége
Alkalmazkodni a nagy sebességű géphez: a most használt tapasz ragasztónak meg kell felelnie a foltbevonat és a nagy sebességű tapaszgép nagy sebességének, azaz a huzalhúzás nélküli nagysebességű pontbevonatnak, vagyis a nagy sebességnek szerelés, nyomtatott tábla az átviteli folyamatban, a ragasztó biztosítja, hogy az alkatrészek ne mozduljanak el.
Huzalhúzás, összeomlás: ha a tapasz ragasztó rátapad a lapra, az alkatrészek nem tudják elérni az elektromos csatlakozást a nyomtatott táblával, ezért a tapasz ragasztó nem lehet huzalhúzás a bevonás során, és a bevonat után nem eshet össze, hogy ne szennyezze a párna.
Alacsony hőmérsékleten történő kikeményedés: Kikeményedéskor a hullámhegyhegesztéssel hegesztett hőálló dugaszolható alkatrészeknek is át kell menniük a visszafolyó hegesztőkemencén, így a keményedési feltételeknek meg kell felelniük az alacsony hőmérsékletnek és a rövid időnek.
Önbeállítás: Az újrafolyós hegesztési és előbevonatolási folyamat során a tapasz ragasztó kikeményszik és rögzítésre kerül, mielőtt a forrasztás megolvadna, így megakadályozza az alkatrész besüllyedését a forrasztóanyagba és az önbeállítást. Erre válaszul a gyártók kifejlesztettek egy önbeálló foltot.
SMT ragasztó gyakori problémák, hibák és elemzések
alátolás
A 0603-as kondenzátor tolóerő követelménye 1,0KG, az ellenállás 1,5KG, a 0805-ös kondenzátor tolószilárdsága 1,5KG, az ellenállás 2,0KG, ami nem éri el a fenti tolóerőt, ami azt jelzi, hogy a szilárdság nem elegendő .
Általában a következő okok okozzák:
1, a ragasztó mennyisége nem elegendő.
2, a kolloid nem 100%-ban kikeményedett.
3, a PCB kártya vagy az alkatrészek szennyezettek.
4, maga a kolloid törékeny, nincs szilárdsága.
Tixotróp instabilitás
Egy 30 ml-es fecskendős ragasztót több tízezerszer kell megütni a légnyomással, hogy elhasználódjon, így magának a tapasz ragasztónak is kiváló tixotrópiájúnak kell lennie, különben a ragasztási pont instabilitását, túl kevés ragasztót okoz, ami elégtelen szilárdságra, ami a hullámforrasztás során az alkatrészek leesését okozza, éppen ellenkezőleg, túl sok a ragasztó mennyisége, különösen a kis alkatrészeknél, könnyen tapad a betét, megakadályozva az elektromos csatlakozásokat.
Nem elegendő ragasztó vagy szivárgási pont
Okok és ellenintézkedések:
1, a nyomtatólapot nem tisztítják rendszeresen, 8 óránként etanollal kell tisztítani.
2, a kolloid szennyeződéseket tartalmaz.
3, a hálótábla nyílása indokolatlanul túl kicsi, vagy az adagolási nyomás túl kicsi, a kialakítás nem elegendő a ragasztóhoz.
4, buborékok vannak a kolloidban.
5. Ha az adagolófej eltömődött, az adagolófúvókát azonnal meg kell tisztítani.
6, az adagolófej előmelegítési hőmérséklete nem elegendő, az adagolófej hőmérsékletét 38 ℃-ra kell állítani.
dróthúzás
Az úgynevezett huzalhúzás az a jelenség, hogy a tapaszragasztó nem törik el az adagolás során, és a tapaszragasztó fonalasan kapcsolódik az adagolófej irányába. Több vezeték van, és a tapasz ragasztója be van fedve a nyomtatott alátétre, ami rossz hegesztést okoz. Különösen, ha a méret nagyobb, ez a jelenség nagyobb valószínűséggel fordul elő, amikor a pont bevonat a szájba. A tapasz ragasztó húzását főként a főkomponens gyanta húzási tulajdonsága és a pontbevonat körülményeinek beállítása befolyásolja.
1, növelje az adagolási löketet, csökkentse a mozgási sebességet, de csökkenti a termelési ütemet.
2, minél alacsonyabb az anyag viszkozitása, magas tixotrópiája, annál kisebb a hajlam a rajzolásra, ezért próbáljon meg ilyen tapasz ragasztót választani.
3, a termosztát hőmérséklete valamivel magasabb, kénytelen az alacsony viszkozitású, magas tixotróp tapasz ragasztóhoz igazítani, majd vegye figyelembe a tapasz ragasztó tárolási idejét és az adagolófej nyomását is.
barlangászat
A tapasz folyékonysága összeomlást okoz. Az összeomlással járó gyakori probléma az, hogy a foltbevonat túl sokáig történő elhelyezése összeomlást okoz. Ha a ragasztót a nyomtatott áramköri lap alátétére húzzák, az rossz hegesztést okoz. És a tapasz ragasztó összeesése a viszonylag magas csapokkal rendelkező alkatrészeknél nem érinti az alkatrész törzsét, ami elégtelen tapadást okoz, így a könnyen összeeső tapasz ragasztó összeesési sebessége nehezen megjósolható, így a pontbevonat mennyiségének kezdeti beállítása is nehézkes. Ennek tükrében olyanokat kell választanunk, amelyeket nem könnyű összecsukni, vagyis a relatíve magas shake oldatot tartalmazó tapaszt. A foltbevonás utáni túl hosszú felhelyezés okozta összeomlás esetén a foltbevonat után rövid idővel elkészíthetjük a tapasz ragasztót, elkerülve a kikeményedést.
Komponens eltolás
Az alkatrészeltolás egy nemkívánatos jelenség, amely könnyen előfordulhat a nagy sebességű SMT gépekben, és ennek fő okai a következők:
1, a nyomtatott tábla nagysebességű mozgása az XY irányban, amelyet az eltolás okoz, a kis alkatrészek tapasz-ragasztó bevonatának területe hajlamos erre a jelenségre, ennek oka az, hogy a tapadást nem okozza.
2, a komponensek alatti ragasztó mennyisége inkonzisztens (például: a két ragasztási pont az IC alatt, az egyik ragasztási pont nagy, a másik pedig kicsi), a ragasztó szilárdsága kiegyensúlyozatlan hevítéskor és kikeményedéskor, és a vége kevesebb ragasztóval könnyen eltolható.
Hullámos részek leforrasztása
Az okok összetettek:
1. A tapasz tapadóereje nem elegendő.
2. Hullámforrasztás előtt érintették.
3. Egyes alkatrészeken több maradvány található.
4, a kolloid nem ellenáll a magas hőmérsékletű hatásoknak
Patch ragasztó keverék
Különböző gyártók tapasz ragasztó a kémiai összetétele van egy nagy különbség, vegyes használat könnyen előállítani egy csomó rossz: 1, keményedési nehézség; 2, a ragasztó relé nem elég; 3, over wave forrasztás le komoly.
A megoldás a következő: alaposan tisztítsa meg a hálótáblát, a kaparót, az adagolót és az egyéb könnyen keveredő részeket, és kerülje a különböző márkájú tapaszragasztók keverését.