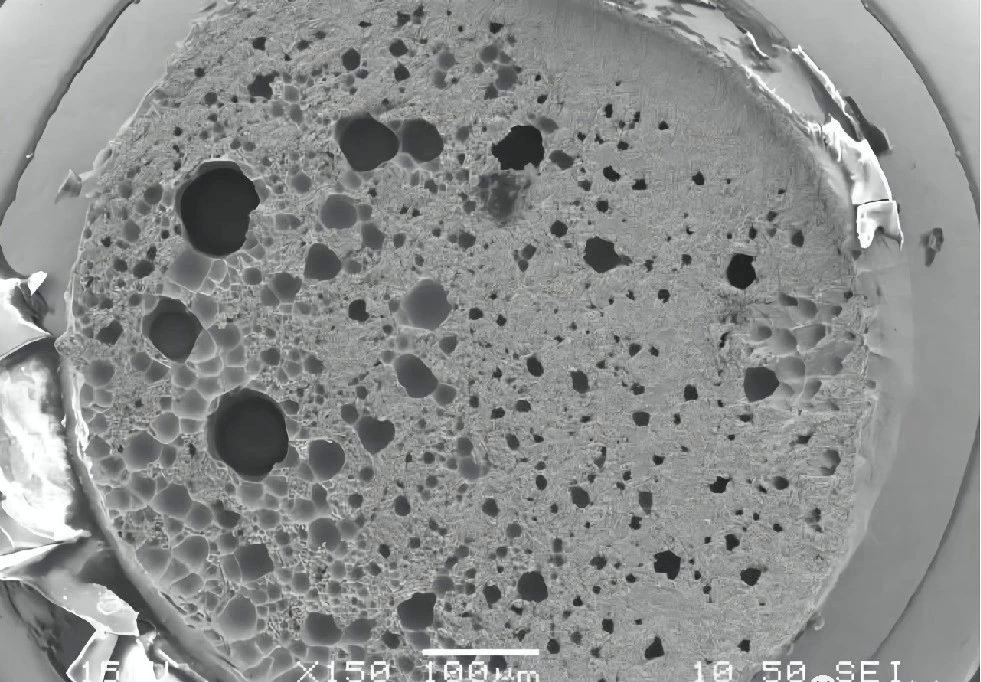
1 Bevezetés
Az áramköri lap szerelvényében először forrasztópasztát nyomtatnak az áramköri lap forrasztólapjára, majd különféle elektronikus alkatrészeket rögzítenek. Végül a visszafolyó kemence után a forrasztópasztában lévő ónszemcséket megolvasztják, és mindenféle elektronikus alkatrészt és az áramköri lap forrasztóbetétjét összehegesztik, hogy megvalósítsák az elektromos részmodulok összeállítását. A felszíni szerelési technológiát (sMT) egyre gyakrabban használják a nagy sűrűségű csomagolási termékekben, mint például a rendszerszintű csomagokban (siP), a ballgridarray (BGA) eszközökben és a power bare Chip, négyzet alakú lapos tű nélküli csomagolásban (quad aatNo-lead, a továbbiakban QFN). ) eszköz.
A forrasztópaszta-hegesztési eljárás és anyagok sajátosságaiból adódóan ezeknek a nagy forrasztófelületű eszközöknek a visszafolyós hegesztése után lyukak keletkeznek a forrasztási területen, ami befolyásolja a termék elektromos tulajdonságait, termikus tulajdonságait és mechanikai tulajdonságait. akár a termék meghibásodásához is vezethet, ezért a forrasztópaszta visszafolyó hegesztési üregének javítása folyamat és műszaki probléma, amelyet meg kell oldani, egyes kutatók elemezték és tanulmányozták a BGA forrasztógolyó okait hegesztési üreg, és a biztosított fejlesztési megoldások, a hagyományos forrasztópaszta visszafolyó hegesztési eljárás 10 mm2-nél nagyobb QFN hegesztési terület vagy 6 mm2-nél nagyobb hegesztési felület hiányzik a csupasz forgács megoldása.
Használjon Preformsolder hegesztést és vákuum reflux hegesztést a hegesztési furat javítására. Az előregyártott forrasz speciális felszerelést igényel a pontszerű folyasztószerhez. Például a chip eltolódik és komolyan megdől, miután a chipet közvetlenül az előregyártott forraszanyagra helyezték. Ha a folyasztószer-rögzítő chip visszafolyós, majd pontszerű, akkor a folyamat két visszafolyással nő, és az előregyártott forrasztóanyag és folyasztószer ára sokkal magasabb, mint a forrasztópasztaé.
A vákuum-visszafolyó berendezés drágább, a független vákuumkamra vákuumkapacitása nagyon alacsony, a költségteljesítmény nem magas, és az ón fröccsenő problémája súlyos, ami fontos tényező a nagy sűrűségű és kis osztású termékek alkalmazásában termékek. Ebben a cikkben a hagyományos forrasztópaszta visszafolyásos hegesztési eljáráson alapuló új másodlagos visszafolyó hegesztési eljárást fejlesztettek ki és vezettek be a hegesztési üreg javítására, valamint a hegesztési üreg okozta ragasztási és műanyag tömítési repedések problémáinak megoldására.
2 Forrasztópaszta nyomtatás reflow hegesztő üreg és gyártási mechanizmus
2.1 Hegesztési üreg
A visszafolyó hegesztés után a terméket röntgen alatt teszteltük. A hegesztési zónában a világosabb színű lyukak a hegesztési rétegben lévő elégtelen forrasztás miatt alakultak ki, amint az az 1. ábrán látható.
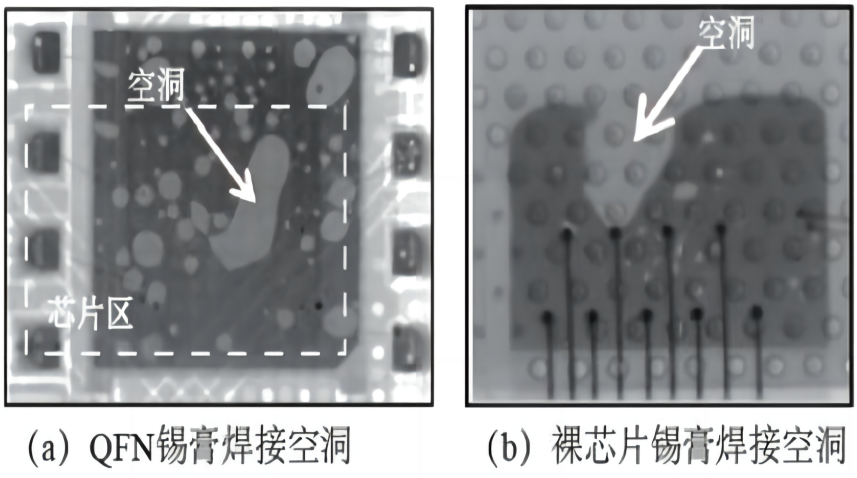
A buboréklyuk röntgensugaras kimutatása
2.2 A hegesztőüreg kialakulásának mechanizmusa
Az sAC305 forrasztópasztát példának vesszük, a fő összetételt és funkciót az 1. táblázat mutatja. A folyasztószer és az ón gyöngyök paszta alakban vannak egymáshoz kötve. Az ónforrasz és a folyasztószer tömegaránya körülbelül 9:1, a térfogatarány pedig körülbelül 1:1.
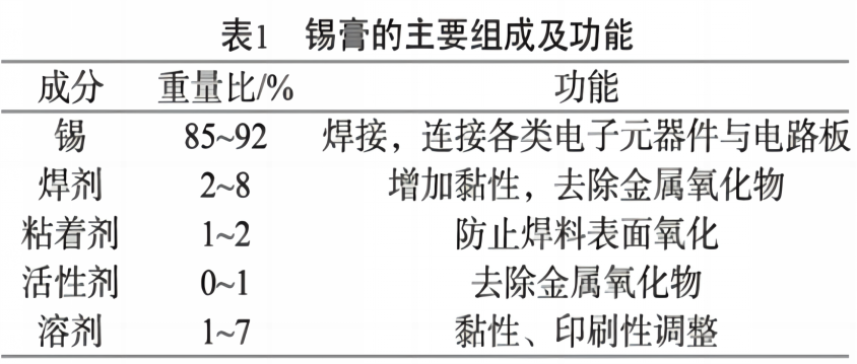
Miután a forrasztópasztát kinyomtatták és különféle elektronikus alkatrészekkel felszerelték, a forrasztópaszta négy szakaszon megy keresztül: előmelegítés, aktiválás, visszafolyatás és hűtés, amikor áthalad a visszafolyató kemencén. A forrasztópaszta halmazállapota is eltérő, különböző hőmérsékletek esetén a különböző szakaszokban, amint az a 2. ábrán látható.
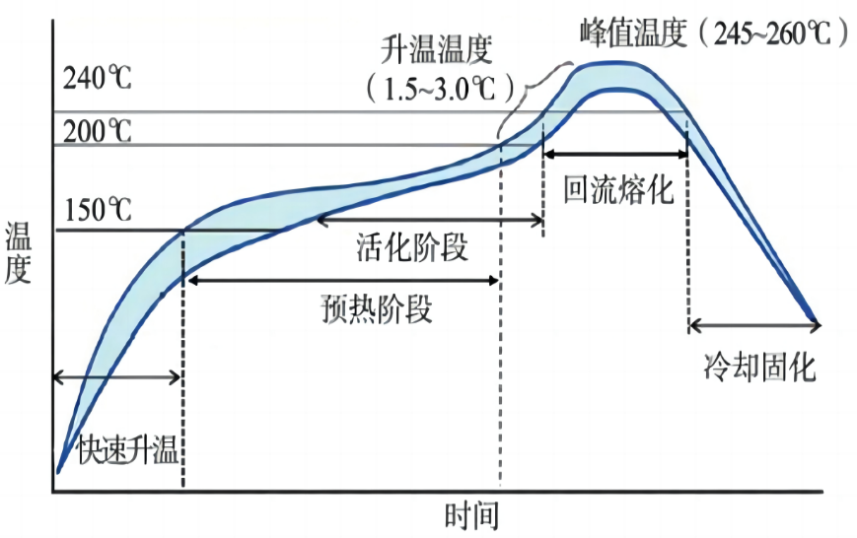
Profilreferencia az újrafolyós forrasztás minden területéhez
Az előmelegítési és aktiválási szakaszban a forrasztópasztában lévő folyasztószer illékony komponensei hevítéskor gázzá párolognak el. Ugyanakkor a hegesztőréteg felületén lévő oxid eltávolításakor gázok keletkeznek. Ezen gázok egy része elpárolog, és elhagyja a forrasztópasztát, és a forrasztógyöngyök szorosan lecsapódnak a folyasztószer elpárolgása miatt. A refluxállapotban a forrasztópasztában visszamaradt folyasztószer gyorsan elpárolog, az óngyöngyök megolvadnak, kis mennyiségű fluxus illékony gáz és a levegő nagy része az óngyöngyök között nem oszlik el időben, és a maradék a forrasztópasztában. megolvadt ón és az olvadt ón feszültsége alatt hamburger szendvics szerkezetű, és megfogja az áramköri lap forrasztóbetétje és az elektronikus alkatrészek, valamint a becsomagolt gáz a folyékony ón csak a felfelé irányuló felhajtóerő miatt nehezen távozik. A felső olvadási idő nagyon rövid. Amikor az olvadt ón lehűl és szilárd ónná válik, a hegesztési rétegben pórusok jelennek meg, és forrasztási lyukak képződnek, ahogy az a 3. ábrán látható.
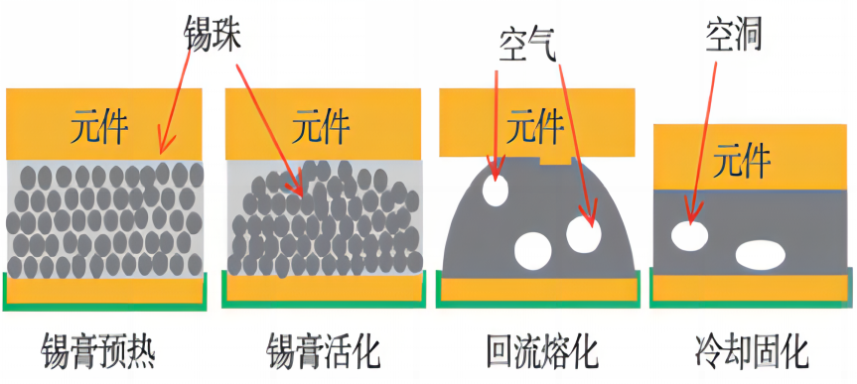
A forrasztópaszta visszafolyásos hegesztése során keletkezett üreg sematikus diagramja
A hegesztési üreg kialakulásának kiváltó oka az, hogy a forrasztópasztába olvadás után a levegő vagy az illékony gáz nem távozik teljesen. A befolyásoló tényezők közé tartozik a forrasztópaszta anyaga, a forrasztópaszta nyomtatási formája, a forrasztópaszta nyomtatási mennyisége, a visszafolyatás hőmérséklete, a visszafolyási idő, a hegesztés mérete, szerkezete és így tovább.
3. Forrasztópaszta nyomtatás visszafolyó hegesztési furatok befolyásoló tényezőinek ellenőrzése
A QFN és a csupasz forgács teszteket használtuk a visszafolyó hegesztési üregek fő okainak megerősítésére, valamint a forrasztópasztával nyomtatott visszafolyó hegesztési üregek javítására. A QFN és a csupasz forrasztópaszta visszafolyó hegesztési termékprofilja a 4. ábrán látható, a QFN hegesztési felület mérete 4,4 mm x 4,1 mm, a hegesztési felület ónozott réteg (100% tisztaságú ón); A csupasz forgács hegesztési mérete 3,0 mm x 2,3 mm, a hegesztési réteg porlasztott nikkel-vanádium bimetál réteg, a felületi réteg vanádium. Az aljzat hegesztőbetétje elektromentes nikkel-palládium aranymerítésű volt, vastagsága 0,4μm/0,06μm/0,04μm. SAC305 forrasztópasztát használnak, a forrasztópaszta nyomtató berendezés a DEK Horizon APix, a reflux kemence berendezés a BTUpyramax150N, a röntgen berendezés a DAGExD7500VR.
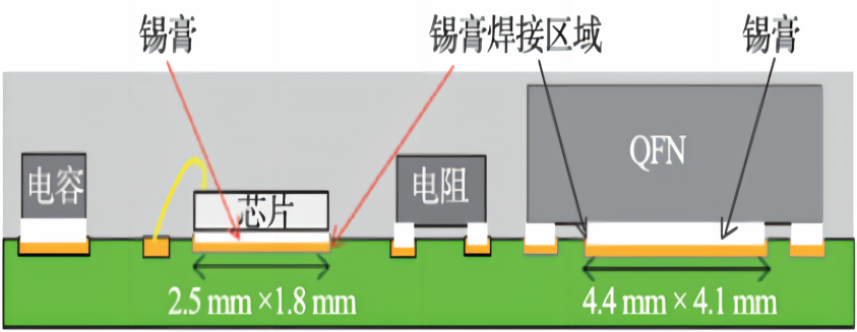
QFN és csupasz forgácshegesztési rajzok
A vizsgálati eredmények összehasonlításának megkönnyítése érdekében a visszafolyó hegesztést a 2. táblázat feltételei szerint végeztük.
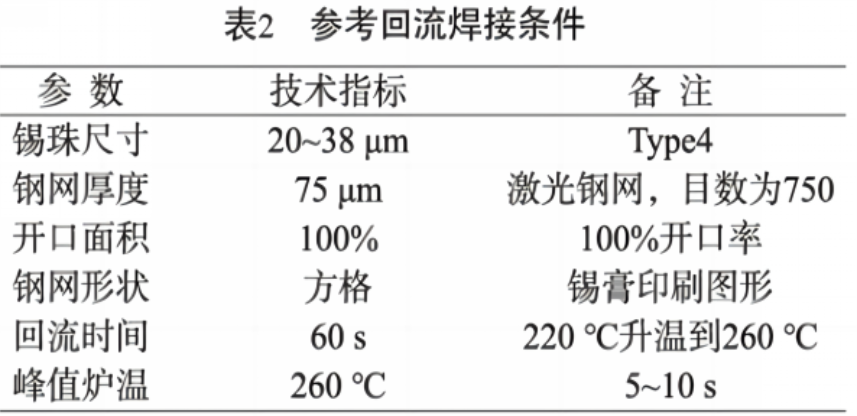
Reflow hegesztési állapot táblázat
A felületi szerelés és a visszafolyó hegesztés befejezése után a hegesztési réteget röntgennel észlelték, és azt találták, hogy a QFN és a csupasz forgács alján nagy lyukak vannak a hegesztőrétegben, ahogy az 5. ábrán látható.
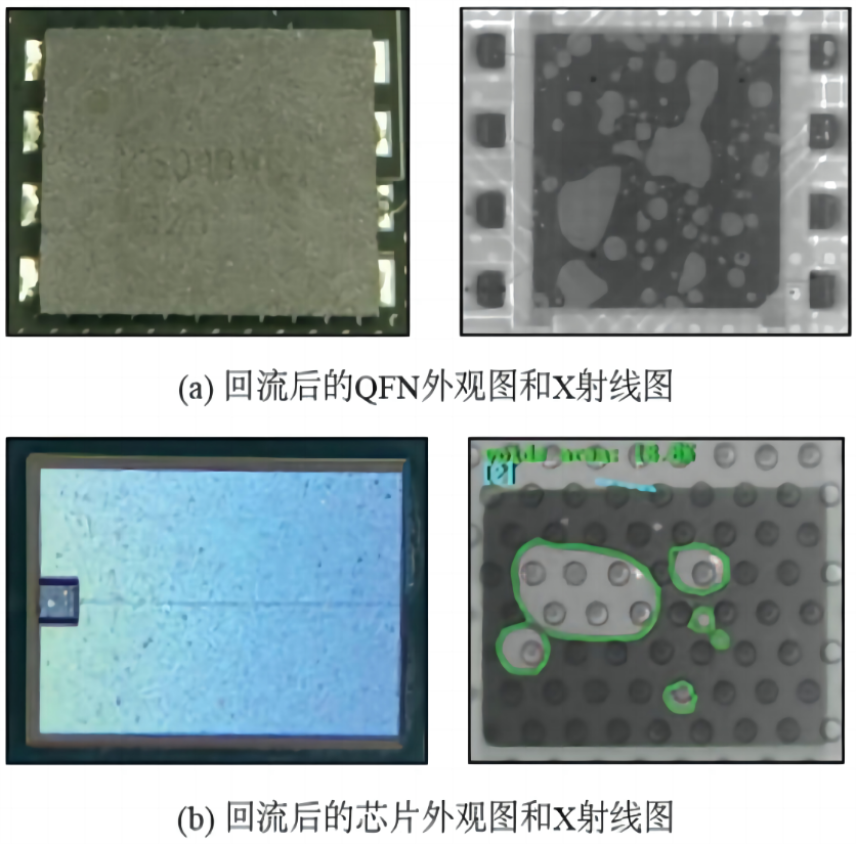
QFN és chip hologram (röntgen)
Mivel az ónszemcsék mérete, az acélháló vastagsága, a nyitási terület sebessége, az acélháló alakja, a visszafolyatás ideje és a kemence csúcshőmérséklete egyaránt befolyásolja a visszafolyó hegesztési üregeket, számos befolyásoló tényező van, amelyeket a DOE-teszt és a kísérletek száma közvetlenül ellenőrizni fog. csoportok túl nagyok lesznek. Szükséges a fő befolyásoló tényezők gyors szűrése és meghatározása korrelációs összehasonlító teszttel, majd a fő befolyásoló tényezők további optimalizálása a DOE-n keresztül.
3.1 Forrasztófuratok és forrasztópaszta óngyöngyök méretei
Type3 (gyöngyméret 25-45 μm) SAC305 forrasztópaszta teszttel a többi körülmény változatlan marad. Visszafolyatás után megmérik a forrasztóréteg furatait, és összehasonlítják a 4-es típusú forrasztópasztával. Megállapítást nyert, hogy a forrasztóréteg furatai nem különböznek szignifikánsan a kétféle forrasztópaszta között, ami azt jelzi, hogy a különböző szemcseméretű forrasztópasztának nincs nyilvánvaló hatása a forrasztóréteg furataira, ami nem befolyásoló tényező. ábrán látható módon. 6 Az ábra szerint.
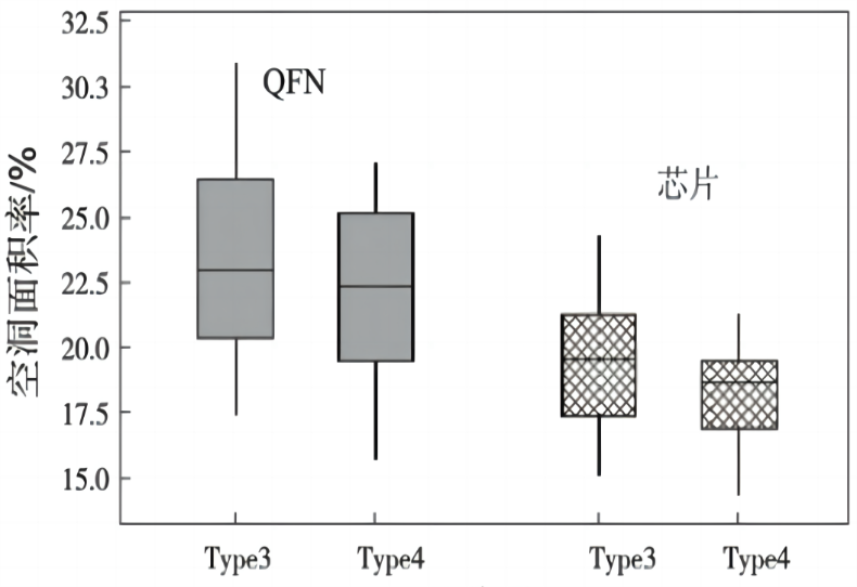
Különböző szemcseméretű fém ónpor lyukak összehasonlítása
3.2 A hegesztőüreg és a nyomtatott acélháló vastagsága
A visszafolyatás után a hegesztett réteg üreges területét 50 μm, 100 μm és 125 μm vastagságú nyomtatott acélhálóval mértük meg, a többi körülmény változatlan maradt. Megállapítottam, hogy a különböző vastagságú acélháló (forrasztópaszta) hatását a QFN-re összehasonlították a 75 μm vastagságú nyomtatott acélhálóéval. Az acélháló vastagságának növekedésével az üreg területe fokozatosan csökken. Egy bizonyos vastagság (100 μm) elérése után az üreg területe megfordul, és az acélháló vastagságának növekedésével növekedni kezd, amint az a 7. ábrán látható.
Ez azt mutatja, hogy a forrasztópaszta mennyiségének növelésével a visszafolyó folyékony ónt befedi a forgács, és a maradék levegő kivezető nyílása csak négy oldalon szűk. A forrasztópaszta mennyiségének megváltoztatásakor a maradék levegő kiáramlása is megnő, és a folyékony ónba csomagolt levegő azonnali felrobbanása vagy a folyékony ónból kilépő illékony gáz folyékony ón fröccsenését okozza a QFN és a forgács körül.
A teszt megállapította, hogy az acélháló vastagságának növekedésével a levegő vagy az illékony gáz kiszökése okozta buborékkitörés is nő, és ennek megfelelően nő a QFN és forgács körüli ón fröccsenésének valószínűsége is.
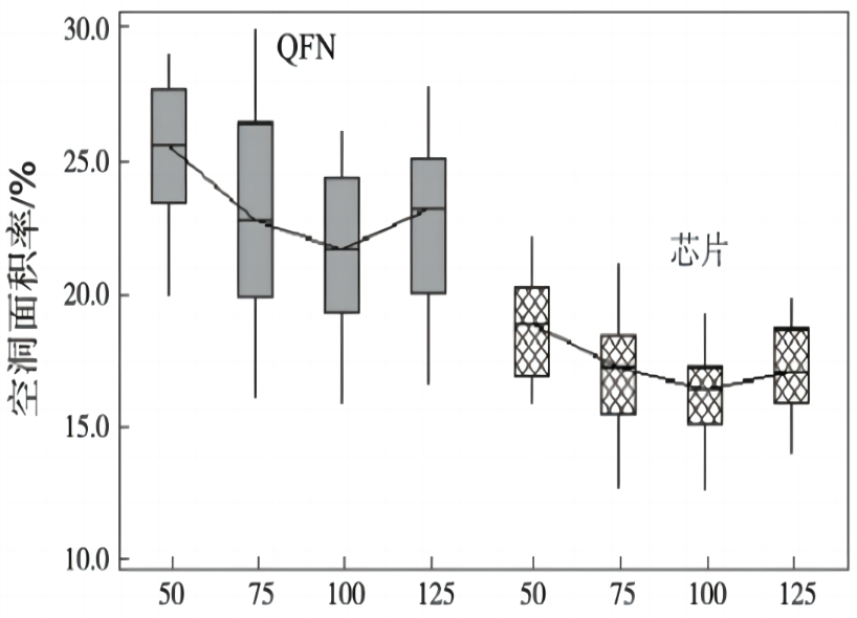
Különböző vastagságú acélhálók furatainak összehasonlítása
3.3 A hegesztőüreg és az acélhálós nyílás területi aránya
A 100%-os, 90%-os és 80%-os nyitási arányú nyomtatott acélhálót tesztelték, az egyéb feltételek változatlanok maradtak. A visszafolyatás után megmértük a hegesztett réteg üreges területét, és összehasonlítottuk a nyomtatott acélhálóval a 100%-os nyitási sebesség mellett. Megállapítást nyert, hogy a hegesztett réteg üregében nem volt szignifikáns különbség a 100%-os és a 90%-os 80%-os nyitási sebesség mellett, amint az a 8. ábrán látható.
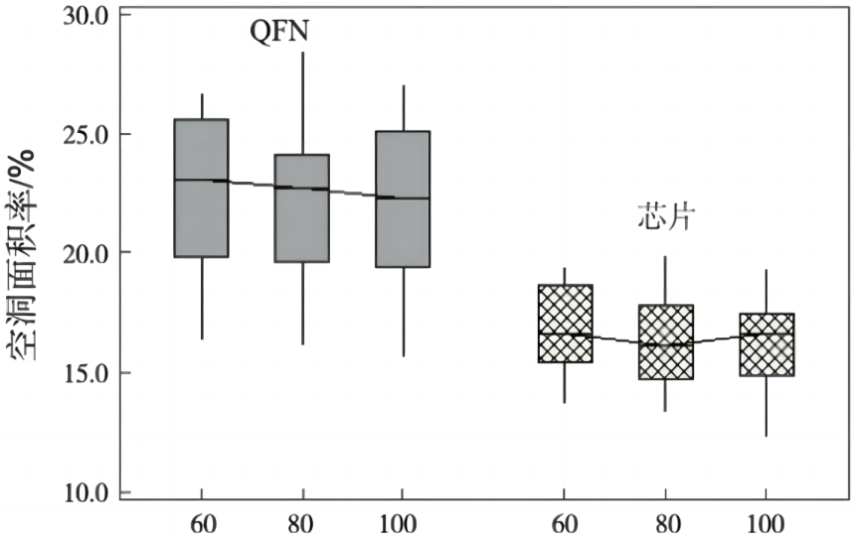
Különböző acélhálók különböző nyílásfelületeinek üreg összehasonlítása
3.4 Hegesztett üreg és nyomtatott acélháló forma
A b szalag és a c ferde rács forrasztópasztájának nyomdai alakpróbájánál a többi körülmény változatlan marad. A visszafolyatás után megmérjük a hegesztőréteg üreges területét és összehasonlítjuk az a rács nyomtatási alakjával. Megállapítást nyert, hogy a 9. ábrán látható módon nincs jelentős különbség a hegesztőréteg üregében a rács, a szalag és a ferde rács körülményei között.
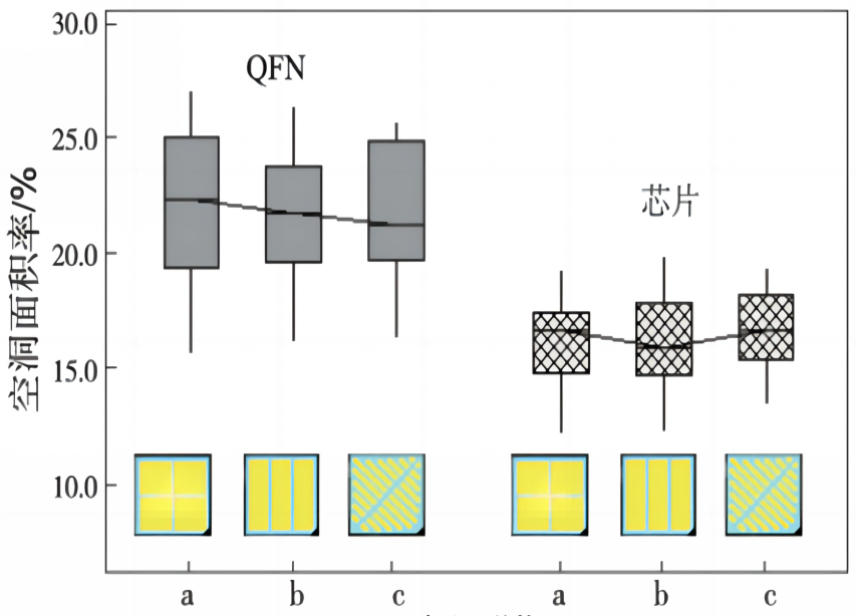
Furatok összehasonlítása az acélháló különböző nyitási módjaiban
3.5 Hegesztési üreg és refluxidő
Hosszabb refluxidő (70 s, 80 s, 90 s) vizsgálat után a többi körülmény változatlan marad, a hegesztőréteg lyukát visszafolyatás után mértük, és a 60 s-os refluxidővel összehasonlítva azt tapasztaltuk, hogy visszafolyási idő alatt a hegesztési furat területe csökkent, de a redukciós amplitúdó az idő növekedésével fokozatosan csökkent, ahogy az a 10. ábrán is látható. elégtelen visszafolyási idő, a refluxidő növelése kedvez az olvadt folyékony ónba csomagolt levegő teljes túlcsordulásának, de a visszafolyási idő egy bizonyos időre való növekedése után a folyékony ónba csomagolt levegő nehezen tud újra túlfolyni. A refluxidő a hegesztési üreget befolyásoló egyik tényező.
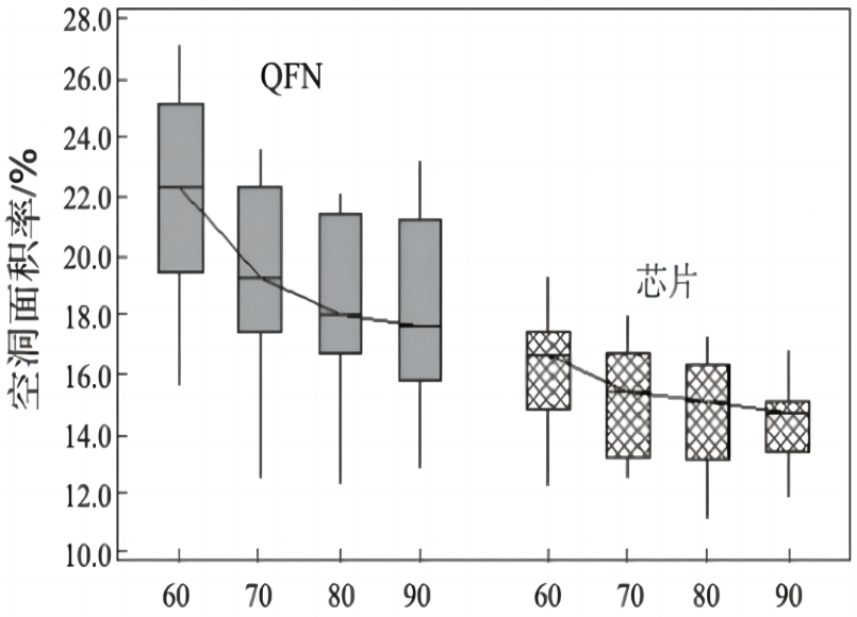
A különböző refluxidő-hosszúságok érvénytelen összehasonlítása
3.6 A hegesztési üreg és a kemence csúcshőmérséklete
240 ℃-os és 250 ℃-os kemence csúcshőmérséklet-teszt és egyéb feltételek változatlansága mellett megmértük a hegesztett réteg üregének területét visszafolyás után, és a 260 ℃-os kemence csúcshőmérsékletével összehasonlítva azt találtuk, hogy eltérő kemence csúcshőmérséklet-viszonyok között az üreg a QFN és forgács hegesztett rétege nem változott szignifikánsan, amint az a 11. ábrán látható. Ez azt mutatja, hogy eltérő csúcs a kemence hőmérsékletének nincs nyilvánvaló hatása a QFN-re és a forgács hegesztőrétegében lévő lyukra, ami nem befolyásoló tényező.
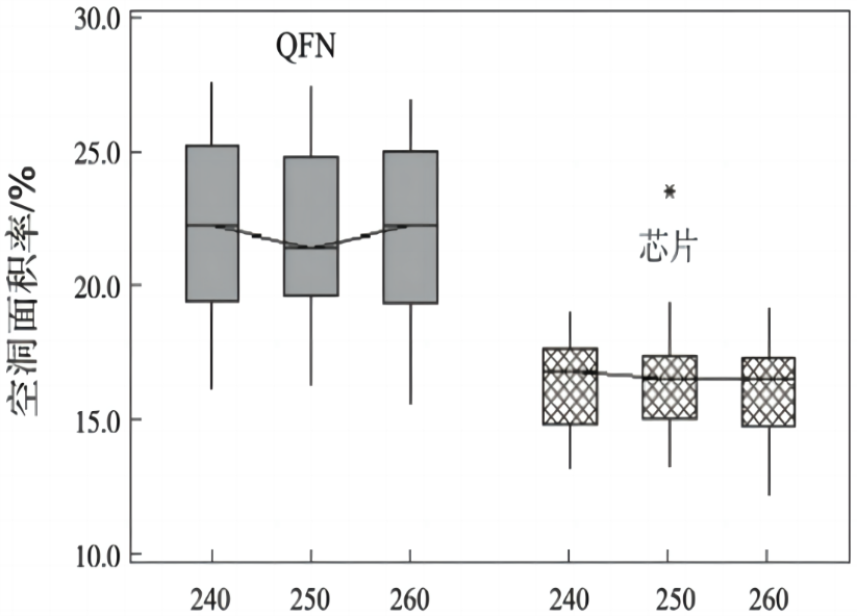
A különböző csúcshőmérsékletek érvénytelen összehasonlítása
A fenti vizsgálatok azt mutatják, hogy a QFN és forgács hegesztési rétegének üregét befolyásoló jelentős tényezők a refluxidő és az acélháló vastagsága.
4 Forrasztópaszta nyomtatás reflow hegesztési üreg javítása
4.1 DOE teszt a hegesztési üreg javítására
A QFN és forgács hegesztési rétegében a lyukat javítottuk a fő befolyásoló tényezők (refluxidő és acélháló vastagság) optimális értékének megtalálásával. A forrasztópaszta SAC305 típusú4, az acélháló alakú rácsos (100%-os nyitási fok), a kemence csúcshőmérséklete 260 ℃ volt, és egyéb vizsgálati körülmények megegyeztek a tesztberendezésével. A DOE tesztet és az eredményeket a 3. táblázat mutatja be. Az acélháló vastagságának és a visszafolyási időnek a QFN-re és a forgácshegesztő furatokra gyakorolt hatását a 12. ábra mutatja. A fő befolyásoló tényezők kölcsönhatás-elemzése révén kiderült, hogy 100 μm-es acélháló vastagság használatával és a 80 s visszafolyási idő jelentősen csökkentheti a QFN és a forgács hegesztési üregét. A QFN hegesztési üregének aránya a maximális 27,8%-ról 16,1%-ra, a forgács hegesztési üregének aránya pedig a maximális 20,5%-ról 14,5%-ra csökken.
A teszt során 1000 terméket állítottak elő az optimális körülmények között (100 μm acélháló vastagság, 80 s visszafolyási idő), és véletlenszerűen megmértük a 100 QFN és forgács hegesztési üreg sebességét. A QFN átlagos hegesztési üregének aránya 16,4%, a forgács átlagos hegesztési üregessége 14,7% A forgács és a forgács hegesztési üregének aránya nyilvánvalóan csökken.
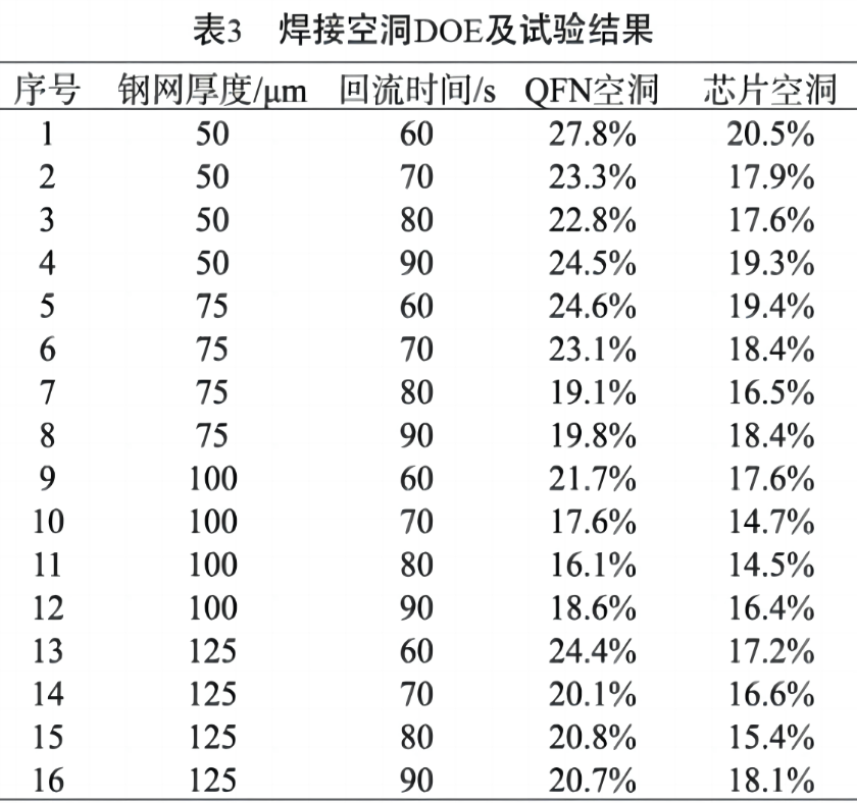
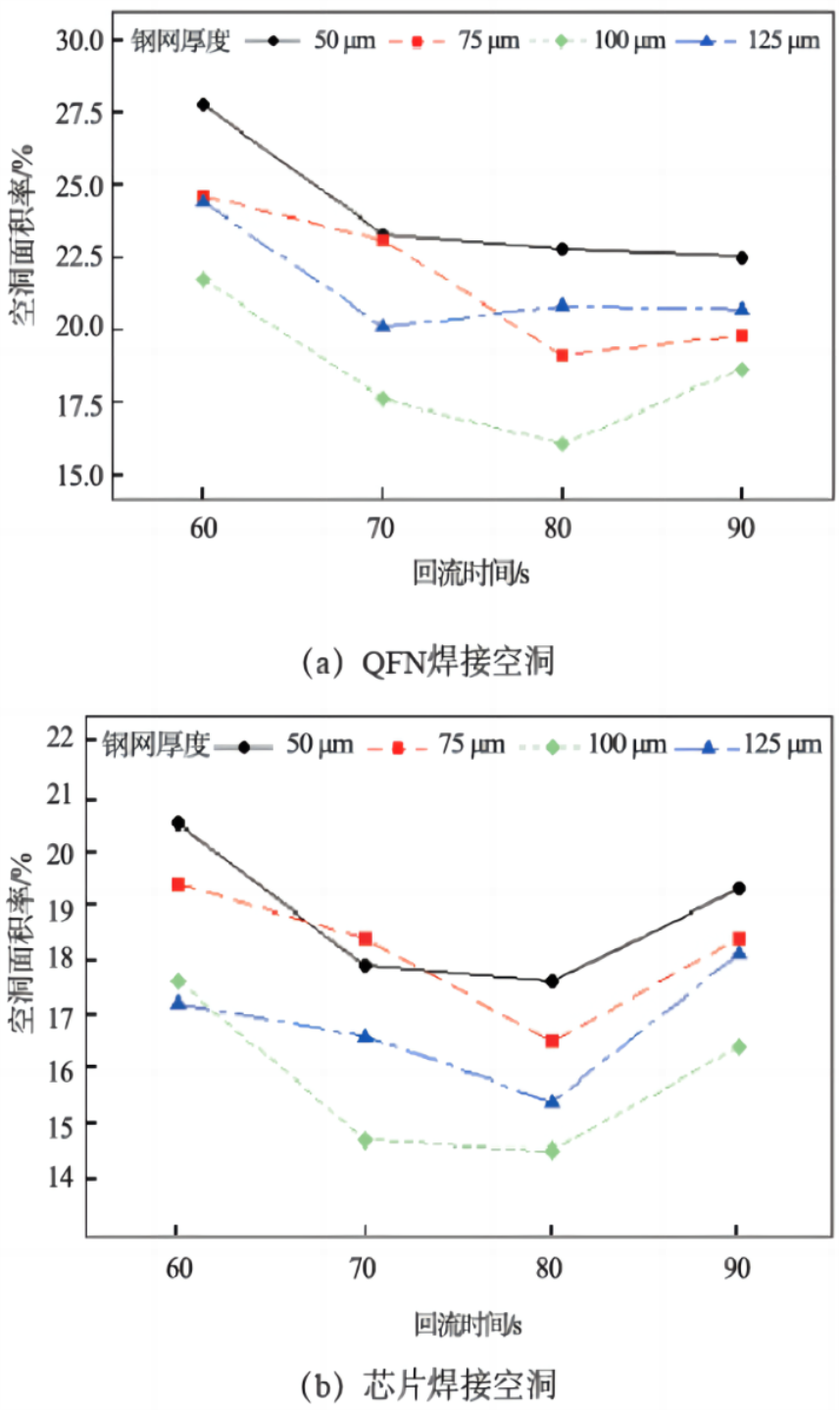
4.2 Az új eljárás javítja a hegesztési üreget
A tényleges gyártási helyzet és a teszt azt mutatja, hogy ha a forgács alján a hegesztési üreg területe kevesebb, mint 10%, a forgácsüreg helyzetének repedési problémája nem fordul elő az ólomragasztás és öntés során. A DOE által optimalizált folyamatparaméterek nem felelnek meg a hagyományos forrasztópaszta visszafolyásos hegesztési lyukak elemzésének és megoldásának követelményeinek, és a forgács hegesztési üregének területi arányát tovább kell csökkenteni.
Mivel a forraszanyagra borított forgács megakadályozza a forraszanyagban lévő gáz eltávozását, a forrasztással bevont gáz eltávolításával vagy csökkentésével tovább csökken a forrasztóanyag alján lévő lyukak aránya. A reflow hegesztés új eljárását alkalmazzák két forrasztópaszta nyomtatással: egy forrasztópaszta nyomtatás, egy újrafolyatás, amely nem fedi le a QFN-t, és csupasz forgács kiüríti a forraszban lévő gázt; A másodlagos forrasztópaszta nyomtatás, tapasz és másodlagos reflux konkrét folyamatát a 13. ábra mutatja.
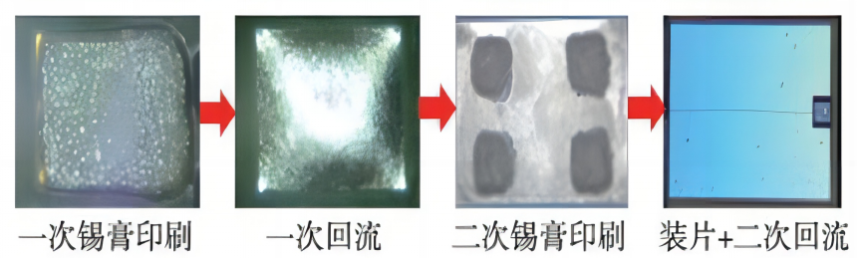
A 75 μm vastag forrasztópaszta első nyomtatásakor a forraszanyagban forgácsfedő nélküli forraszanyagban lévő gáz nagy része kiszökik a felületről, és a vastagság visszafolyatás után körülbelül 50 μm. A primer visszafolyatás befejezése után a lehűtött megszilárdult forrasz felületére kis négyzeteket nyomtatnak (a forrasztópaszta mennyiségének csökkentése, a gáz kifolyásának csökkentése, a forrasztási fröccsenés csökkentése vagy megszüntetése érdekében), és a forrasztópaszta 50 μm vastagság (a fenti vizsgálati eredmények azt mutatják, hogy a 100 μm a legjobb, tehát a másodlagos nyomtatás vastagsága 100 μm.50 μm=50 μm), majd helyezze be a chipet, majd térjen vissza 80 másodpercen keresztül. Szinte nincs lyuk a forrasztóanyagban az első nyomtatás és visszafolyatás után, a második nyomtatásnál pedig kicsi a forrasztópaszta, kicsi a hegesztési lyuk, ahogy az a 14. ábrán látható.
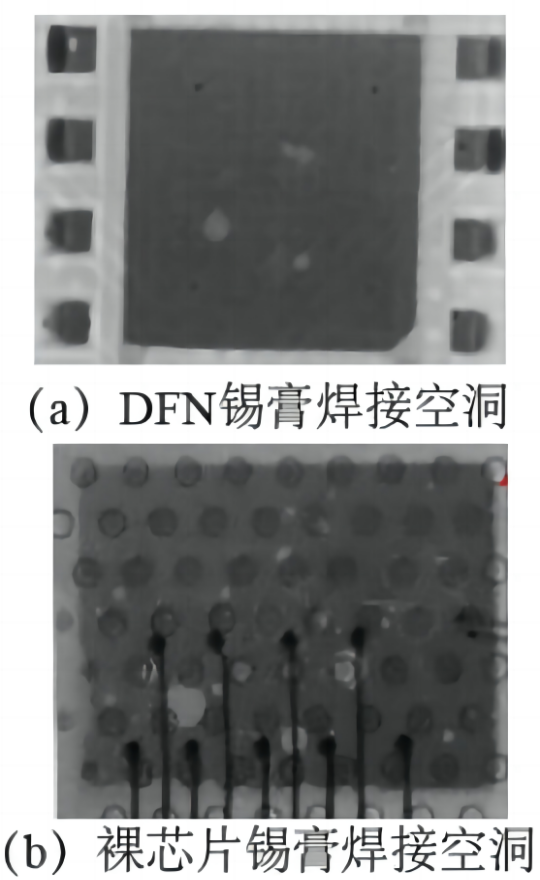
Két forrasztópaszta nyomat után üreges rajz
4.3 A hegesztési üreg hatásának ellenőrzése
2000 termék gyártása (az első nyomóacél háló vastagsága 75 μm, a második nyomóacél háló vastagsága 50 μm), egyéb feltételek változatlanok, véletlenszerű 500 QFN mérés és forgácshegesztési üreg arány, megállapították, hogy az új eljárás az első reflux után nincs üreg, a második reflux után QFN A hegesztési üreg maximális aránya 4,8%, és a maximális a forgács hegesztési üregének aránya 4,1%. Összehasonlítva az eredeti egypasztás nyomtatási hegesztési eljárással és a DOE optimalizált eljárással, a hegesztési üreg jelentősen csökkent, amint az a 15. ábrán látható. Az összes termék funkcionális tesztelése során nem találtunk forgácsrepedést.
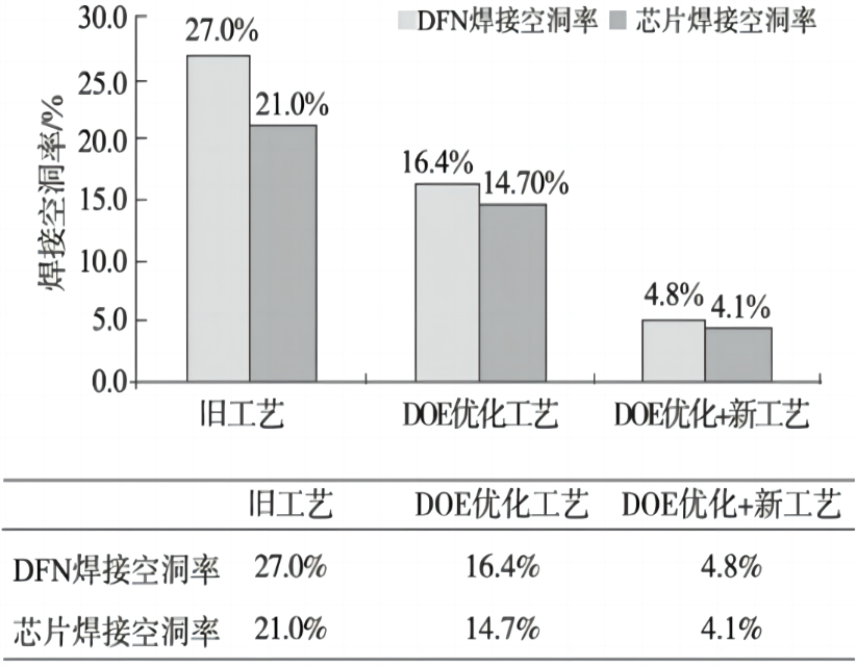
5 Összefoglalás
A forrasztópaszta nyomtatási mennyiségének és a visszafolyási időnek az optimalizálása csökkentheti a hegesztési üreg területét, de a hegesztési üreg aránya továbbra is nagy. Két forrasztópaszta nyomtatási reflow hegesztési technikával hatékonyan és maximalizálható a hegesztési üreg aránya. A QFN áramköri csupasz forgács hegesztési területe tömeggyártásban 4,4 mm x 4,1 mm, illetve 3,0 mm x 2,3 mm lehet. A visszafolyó hegesztés üreges sebességét 5% alá szabályozzák, ami javítja a visszafolyó hegesztés minőségét és megbízhatóságát. A jelen cikkben szereplő kutatások fontos referenciaként szolgálnak a nagy felületű hegesztési felületek hegesztési üreg problémáinak javításához.
Feladás időpontja: 2023.05.05